A digital path to perfection
Achieving high set goals require a great ability to translate vision into practice. And when The Absolut Company’s ambitious sustainability goals are to become a reality, two of the keys are to both improve and refine the machines and processes – without this affecting production.
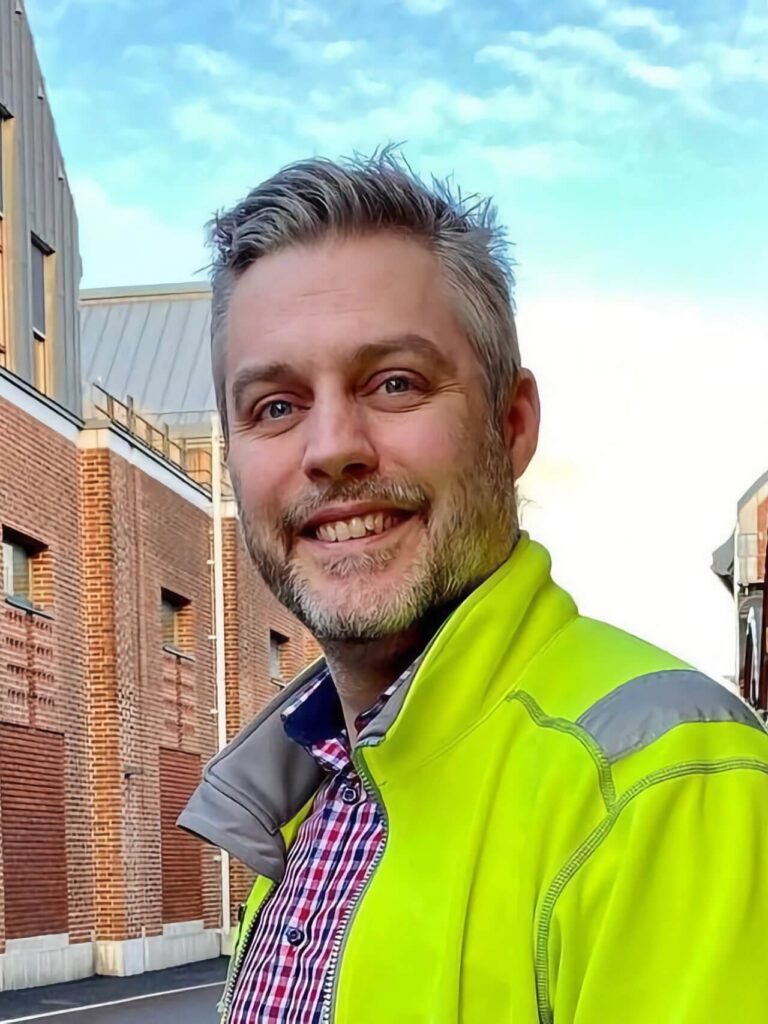
The solution is to build a digital copy of the factory in order to be able to test and analyze changes virtually. We had a short chat with automation engineer Emil Svärdh about what he actually does at work every day and why it is so important.
Your title is Senior Automation Engineer. What does that mean?
That is a good question. The simple answer is that I work with our journey to become autonomous – that is, with the digitalisation of our production. I don’t really work with our machines, but more with information flow to and from the machines. Primarily by building a digital replica of our physical flows. In this way, it is easier to see and analyze what is happening in production in order to then be able to make changes and improvements in the real machines. In other words, I sit in front of a computer and set up an architecture of which systems and data points to include, which system should own which data point and how they can be orchestrated internally to business systems or manufacturing systems. It sounds a bit abstract, but when I can show what a change means, it usually clears up. The data we extract shall be used to support our decision making and continuous improvements.
The data we extract shall be used to support our decision making and continuous improvements
What are the benefits of automation?
Our production philosophy includes that we are One source – that we come from and are manufactured in one place. This allows us to look at the entire flow of production and thus be very agile in finding new ways to refine and improve our processes. Both when it comes to manufacturing and waste management. Making a Litre Absolut Vodka is a simple thing, but if you change something only a little bit in the manufacturing process, it will generate a new digital path that needs to be controlled before the product can be manufactured. And that’s my job.
How far has TAC come in the development of digitalisation?
We are extremely far ahead in an automation perspective. It also means that we have an easier journey than many others. We have got off to a good start thanks to the fact that we have new machines and financial means – but also because we have a management that is interested in us making this journey and an organization that can and wants to be a part of it.

How do you work with AI and Machine Learning when it comes to automation?
AI and Machine Learning is really an upcoming project for us. Today, it is most introduced through predictive maintenance of components in the machines. When it comes to bottling, we are in the starting blocks, but in order for it to be fully implemented, we must first know exactly what we produce and how we produce it from a digital point of view. We are building up that knowledge base right now and when we have all the facts, we can apply AI and machine learning fully. An example of this is how we work with our glass. It is a living material, so that makes it a perfect starting point for applying machine learning in order to be able to avoid sorting out glass that is not incorrect, although the reflection may look like that to the vision system we have. Here, the operator is a key player for us building a reference model of what is a good versus scrap. It takes time to gather all the knowledge, but once it is done, it will definitely impact the production.
AI and Machine Learning is really an upcoming project for us
What other industries are leading this development?
I would say that the car industry is the one that has come the furthest. Another player is Swedish ball bearing manufacturer SKF. There is a big difference compared to our business though – these industries have an aftermarket that must be taken into account, which is not the case for us. On the other hand, we want to adopt the same basic idea, that is, that we do not just make a product, hence the product itself is a variety of components and operations to be performed. If we think like that, it will be easier to break down our processes and find a digital path to the end product that is flexible. Once we get there, we can also more easily make the changes and improvements needed to reach our goals.
How does your work help TAC to achieve its high sustainability goals?
It is about choosing which initiatives to support. To choose the right one, one must first know what the actual reality looks like and then find the best way to be able to control it. That’s very important. My job is also very much about building on our transparency canvas, that is, how we work and what it generates. The result can then be shown to our customers and also be used for improving our work.
What is your vision for production in Åhus in the long term?
To be a “One button shop”. That we should have a ready-made path for all our products – regardless of whether we want to manufacture one or 100,000 units. We must be even more agile to make changes that take the products we produce to market as fast as possible. It is a journey we are in the middle of and I am completely convinced that when we are at the finish line, it will benefit both us as a company and our consumers.