Countdown to being fossil-free
Absolut Vodka continous to work on decreasing carbon thoughout the value-chain.
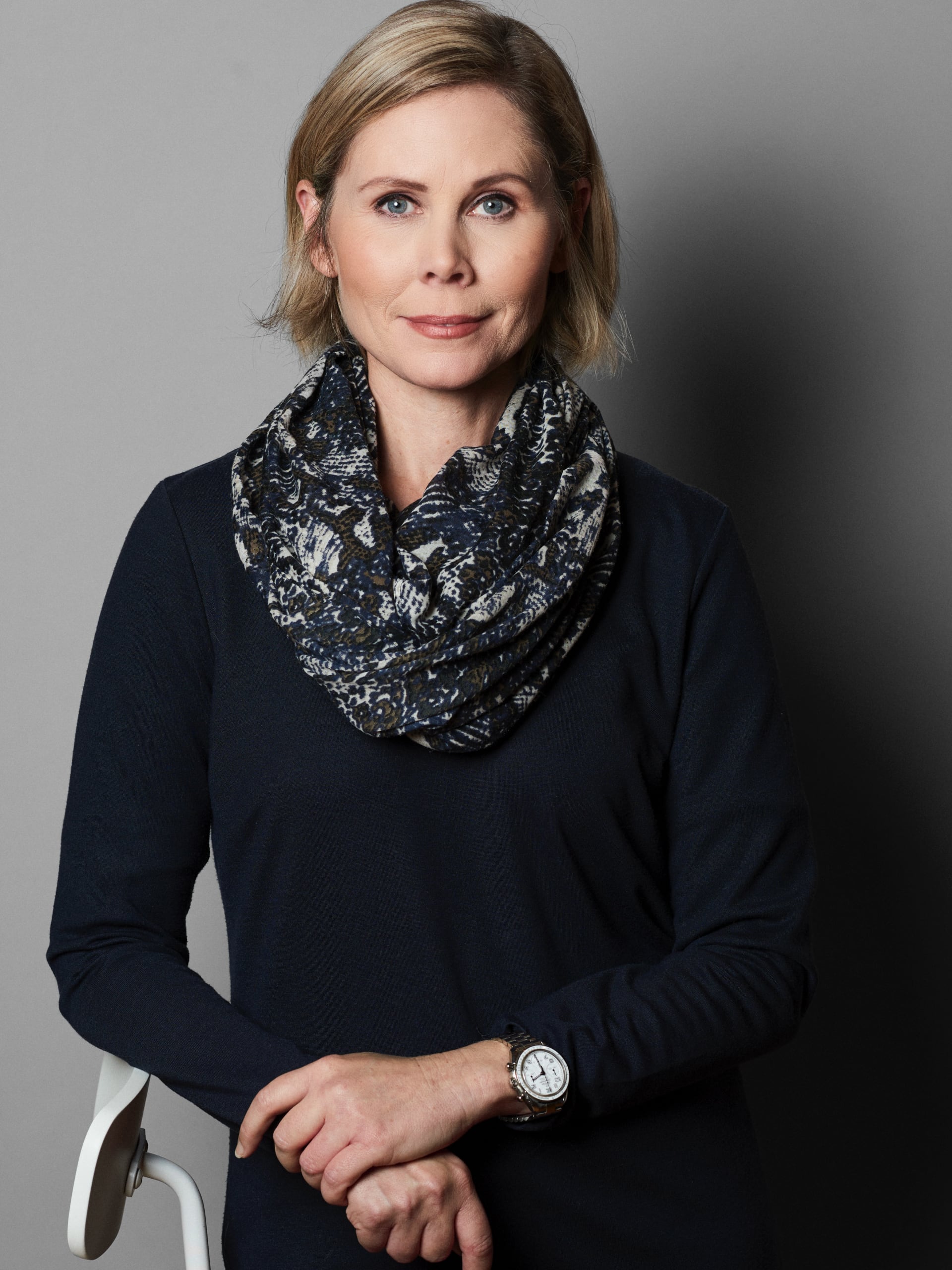
Absolut Vodka’s distillery remains one of the most energy-efficient in the world despite producing its own raw spirit. Not all distilleries produce their own raw spirit, which is a complex and energy-intensive process. Instead, many spirits brands buy spirits from external sources and redistill them. Absolut, using wheat produced by around 300 local farms and water from one of northern Europe’s biggest natural aquifers, makes its raw spirit from scratch. Nevertheless, the distillery in Nöbbelöv, close to Åhus is 87 per cent more carbon efficient and emits seven times less CO2 per litre of alcohol than the average distillery.*
Scope 1 & 2 emissions fell to 103 tonnes in FY24 from 1985 tonnes in FY23, the lowest since Absolut began measuring carbon emissions in 2005. The resulting carbon efficiency of the distillery and bottling was 1 g CO2/I vodka compared to the previous year’s 17 g CO2/I vodka. The strive to reduce emissions further continues. Last year it opened a new two million-litre storage facility that will increase the distillery’s efficiency by better balancing fluctuating demand. The distillery is at its most efficient when it runs continually, something it can now do with storage capacity increased by 20 per cent.
Fossil-free in sight
Absolut has committed to its distillery being fossil-free by 2025 – a goal that Anna Schreil, VP Operations, The Absolut Group, says is “firmly on track”. Today, 92 per cent of the energy used at the distillery comes from green electricity. It uses around 7 per cent green fuel, made in-house using waste spirits such as fusel oils, discarded flavoured vodkas from defective bottles or discontinued products and less than 1 per cent fossil fuel liquefied petroleum gas (LPG).
To achieve its fossil-free goal, Absolut is currently evaluating its options to finally phase out the last remaining fossil fuel. The main energy source of the distillery is electricity. This will most likely be the case also in the future, but there are occasions when extra fuel is needed. One fuel is already available, the waste spirits from the in-house processes, but it doesn’t produce enough to fill the gap left after removing LPG.
Subsequently, Anna and her team are looking at options that include bio-LPG or biogas. In the short term, the solution might be to purchase fuels with a mass balance approach (similar to the system for electricity), where certificates provide proof that the same amount of renewable fuel is input to the grid as Absolut buys to cover its needs. In the long term, Absolut wants to find a ‘physical solution’, meaning that the actual molecules of fuel used at the distillery come from a renewable source.
“Have you bought green energy or invested in green energy? We will not be satisfied until we have a green ‘physical’ solution that guarantees we are using renewable energy. We want to be part of something truly transformational and make a positive impact,” says Anna. “We can buy mass-balanced green LPG or biogas but that is the easy solution rather than the best solution. I believe we have a bigger role to play. We can use what is available to us such as certificates [to become fossil-free] but we also need to ensure that transformation is happening.”
We want to be part of something truly transformational and make a positive impact
Hydrogen furnace
Nearly half of the carbon footprint of Absolut Vodka comes from the natural gas used in the production of the bottle, but an industry ground-breaking initiative is set to change this. Working with Ardagh, its long-term glass bottle supplier, all Absolut will soon be switching to full-scale glass bottle production using hydrogen as an energy source. The move will reduce Absolut Vodka’s carbon footprint for every glass bottle by an estimated 17 per cent and reinforce Absolut’s goal for its premium-quality vodka to eventually become a CO2-neutral product.
“The partly-hydrogen-fired glass furnace is just part of the strategy,” says Anna. “The next step is to build a new hybrid furnace using 20 per cent hydrogen (or biogas) and 80 per cent electricity.”
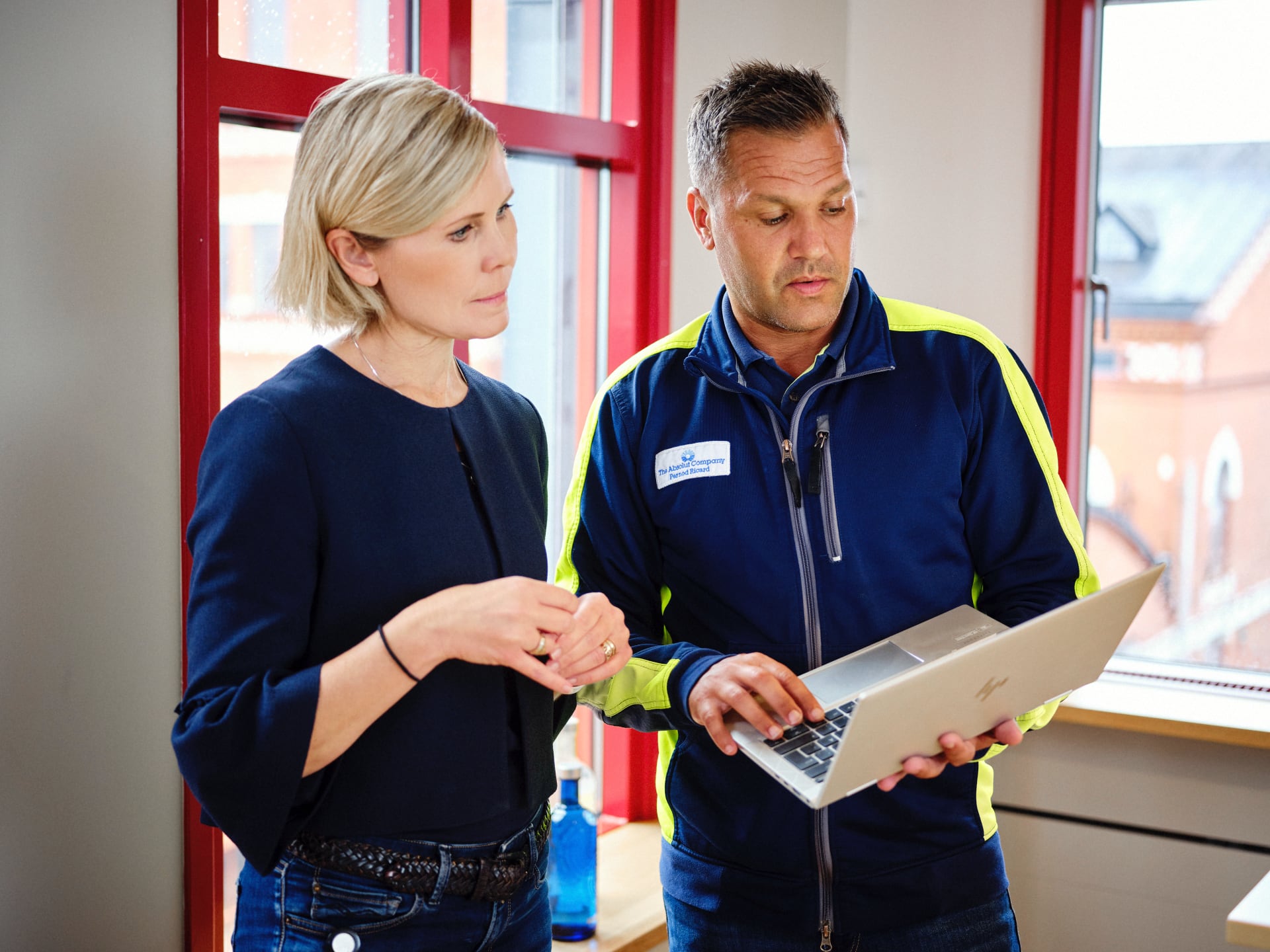
Lighter bottle conundrum
We have already made significant strides in making our iconic glass bottle lighter (by 10 per cent in 2015). A lighter bottle not only reduces the CO2 emissions in the production of the bottles but also on transport (and the costs) because you can transport more bottles per container. We currently use at least 50 per cent recycled glass, known as cullet, in our Absolut Vodka bottles.
“We have taken many steps to make our bottle lighter, but a significant reduction from here could affect the look of the bottle. This is a big decision and it is something we are looking into,” says Anna. “But even a tiny removal of glass can lead to savings beyond the grams of glass that you would take out. All of a sudden, your shipping cases might become a little bit smaller and you can fit one layer more onto the pallet to fit with the maximum height of a container. That’s the optimum that you need to compute and calculate.”
To meet the challenging SBTi targets, we will need to increase our focus on both carbon sequestration and reductions such as with the choice of fertilisers and fuels
Capturing carbon
Carbon capture is a core focus towards achieving Absolut’s goal of being a carbon-neutral product by 2030. As part of the wheat fermenting process, biogenic CO2 (captured from the air by the growing wheat) is released. Around 30 per cent of carbon released from its 10 fermentation tanks is captured, which is then purified and liquefied before being sold to other industries. But Anna wants to capture more. “If we could capture 100 per cent, then wow! And instead of it being just transferred and used somewhere else, we could make sure it is removed from the atmosphere entirely by storage techniques (BECCS) – which are currently being industrialised in our region and essentially ‘locking’ CO2 deep below ground,” adds Anna.
Farming more data
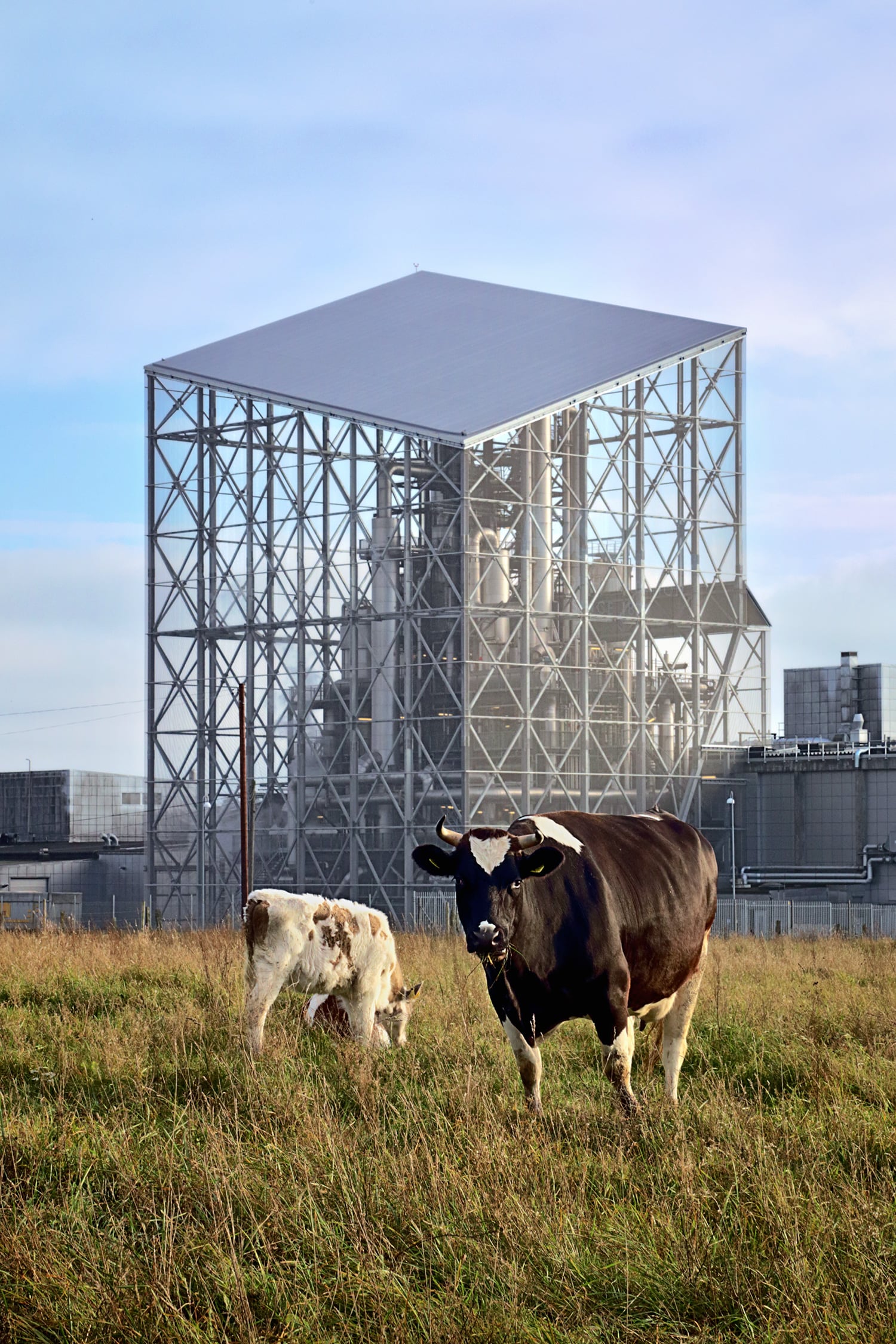
Wheat contributes to a significant part of Absolut Vodka’s total carbon footprint and Absolut works closely with all its farmers encouraging them to make sustainable improvements with an incentivised points-based system. Its Sustainable Wheat Programme encompasses three key themes – climate (to reduce CO2 emissions), soil health (to improve the fertility of the soil and reduce nutrient leakage) and biodiversity (to maintain or create habitats for plants and animals). In 2024, Absolut appointed an audit body to validate the data from the programme’s 300 participating farms.
“This is important because it will improve the quality of the data. We already calculated the emission factor of the wheat every year since 2017 and started taking action but now we can set a better baseline that we feel really confident about,” says Anna.
Absolut is also examining how it can contribute to Pernod Ricard Group’s FLAG targets (30 per cent reduction by 2030). The world’s Forest, Land and Agriculture (FLAG) sector is responsible for approximately 25 per cent of net greenhouse emissions globally, but it also has the potential to absorb a significant number of existing emissions from the atmosphere. To address this gap in emissions accounting and reduction, the Science Based Target Initiative (SBTi) recently introduced new guidance on what actions companies need to take to limit global warming.
“We started the Wheat Sustainability Programme many years ago and have developed a very close co-operation with our farmers so they are aware that we have ambitions and targets in mind,” says Anna. “We have already been working on ‘climate-smart’ fertilisers using best-available technology – and these now account for more than half of fertilisers used in our fields. To meet the challenging SBTi targets, we will need to increase our focus on both carbon sequestration and reductions such as with the choice of fertilisers and fuels.”
* Average data from 2022. Beverage Industries Environmental Roundtable (BIER) benchmarking study.
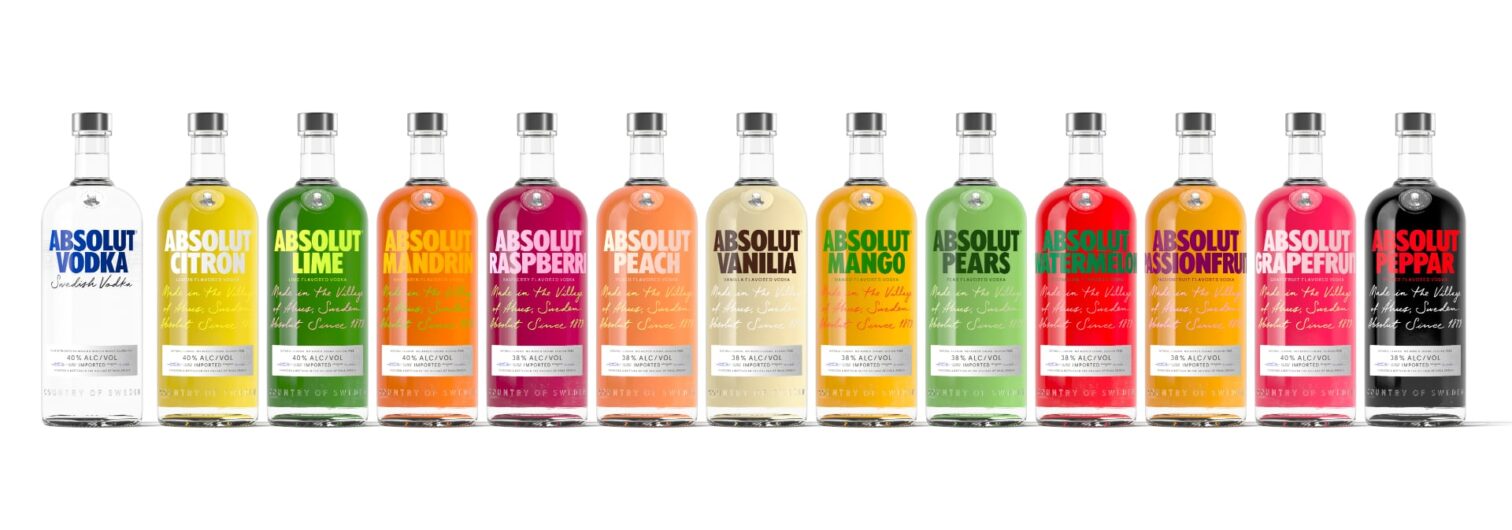