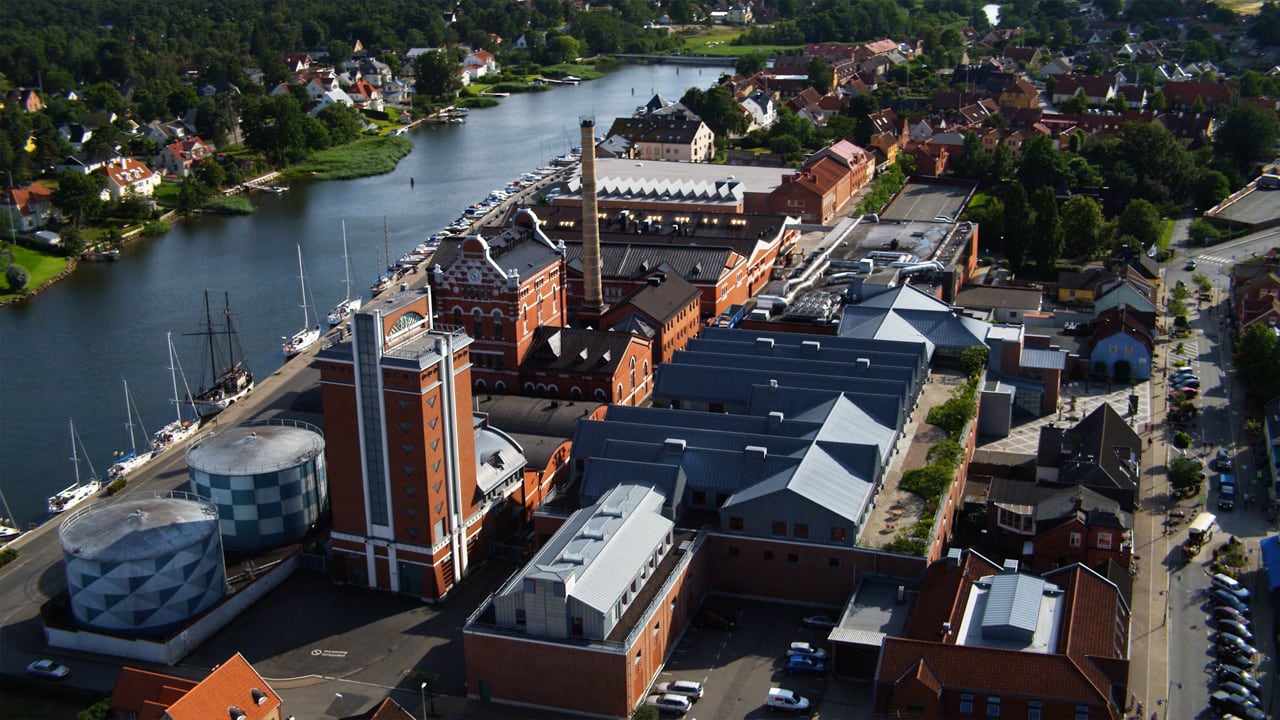
Getting transportation is a challenge
With a global shipping crisis at hand, businesses all over the world are having to adapt to a new normal where transportation is at best unstable and at worst unavailable. This is taking a toll at world trade with low stock of many imported goods in several markets. For consumers, alarming headlines like “Empty shelves at IKEA and Walmart”, and ”Container shortage is threatening Christmas shopping” is everyday news.
But it’s not only furniture, tech and toys that are affected by the lack of shipping vessels and the massive increase in container prices. The global spirits business is equally impacted by the unstable situation. Being Sweden’s largest single food exporter, Absolut does of course also have to consider the logistical challenges. Both in terms of how to transport goods and how to plan for production.
– For us, the primary issues are due to the instability and uncertainty that prevails right now. We can’t really trust that everything we’ve done before still works the same way we’re used to. It’s one thing that we’re able to produce what we are supposed to at the right time, but it is a whole other matter to know for a fact that we actually have containers available to load the cargo. At the moment, it is sometimes a last-minute call, says Peter Neiderud, Head of Planning and Warehousing at The Absolut Company.
The global logistics chain is a complex matter and the pandemic has had a profound impact on the number of vessels available for transportation and, even more importantly, the number of people working to load and unload cargo at the ports. When covid 19 hit the world, many countries shut down and ports and harbors we’re closed or had their access restricted. With the world now once again opening up, the system has a delay and isn’t running at full speed. This means that the capacity to quickly handle all the incoming and outgoing cargo isn’t optimized. Simply put, there’s just too much work and to few people. The effect is that containers are stuck in customs or storage longer than before and a que starts to form. For Absolut, no immediate changes have had to be made, but planning and forecasting has to be done on a more ad-hoc basis from time to time.

Our logistics works like this: we have a feeder boat that embarks Åhus once a week to pick up the loaded containers and carry them down to Hamburg and Bremenhafen. It is from there that the majority of all goods are reloaded to ocean freight carriers that transports the goods around the world. In return, the big carriers bring empty containers with them back to port which our feeder boat brings back to Åhus for re-use. This is the flow that we’re dependent on for the logistics to work. And right now, this is not always really happening, which means that in some cases, some of our customers have to wait a bit longer for their products to arrive. Lead times have increased to 6-7 weeks today, from around 4 weeks in normal circumstances. There is an imbalance in trade between China and the USA that adds to the problematic container shortage. Prices have increased 10-fold due to capacity being so much lower than demand right now, says Peter Neiderud.
Are all transports affected by the logistical challenges?
– We have the privilege of having most of our subcontractors at an arm’s length locally. But we do have some suppliers who are a little further away in, for example, Italy and the UK. Especially in the latter case, there is some concern. They not only have problems in the ports, but also with truck deliveries. This means that we have had to re-plan a bit during the year and produce according to availability. This mainly applies to different spices and flavors, which are sourced from all over the world and thus are extra exposed in several stages of the logistics chain. It becomes a kind of “trickle down” effect where certain lead times are doubled or even tripled.
We have the privilege of having most of our subcontractors at an arm’s length locally. But we do have some suppliers who are a little further away in, for example, Italy and the UK.
Adding to the though internal logistical challenges are also the fact that many suppliers are facing even greater obstacles. Getting hold of produce to refine is sometimes almost impossible due to high demand on the global market. Many businesses are competing for the same type of raw materials and flavorings which has made the prices skyrocket. – All these price mark-ups are affecting our suppliers and we’re lucky to have such good relations with all our partners – and long-term agreements with open books price adjustment formulas – that we can adjust to the changes in the world market together. We are doing our best to be foresighted when calculating the capacity needed and agile to avoid creating bottlenecks that can impact our supply chain, says Johan Blixt, Director Supply Chain at The Absolut Company.
What does this mean for the production in Åhus?
– We’ve had to increase our production rate significantly. During the year, we’ve added capacity equivalent to one full month’s production. This means that all our five lines have run at maximum capacity, and this has never happened before. We do the best we can to make it work and the staff has been fantastic in adapting to the changes and enduring the extra workload. It is done on a voluntary basis and so far we’ve run many extra Saturdays and extended Fridays to compensate for the increase in demand. And we’ve also hired about 25 extra staff to the production to be able to better manage the spike in demand. So, we have our hands full in Åhus right now, that’s for sure.
