
Many small steps make a big difference
Our passion for progression is never more so embraced than at Absolut Vodka’s vast distribution centre in Åhus. Our dozen-strong on-site team is continually examining ways to improve the efficiency and sustainability of an operation that is responsible for distributing 12,7 million cases of Absolut Vodka around the world each year.
“We never stop. We just take small steps all the time,” says Harri Tossavainen, Warehouse and Distribution Manager, The Absolut Company. “We are distributing 10,600 containers of Absolut Vodka around the world and so we must always look to improve – whether that is optimising the number of cases in the containers, looking at a robotic system to load the pallets even tighter or examining different materials to secure pallets.”
The fully automated distribution centre handles Absolut products with conveyors, cranes and shuttles. Such is the advancement of its technology that reduces manual work, seven of the team of 12 have worked in the distribution centre for more than 30 years – a testament to the health and safety standards at Absolut. Five production lines process a maximum of around 1,600 pallets Monday to Friday. The only part of the process that is not automated is final loading, which is done by forklifts, although there are plans for this to change.
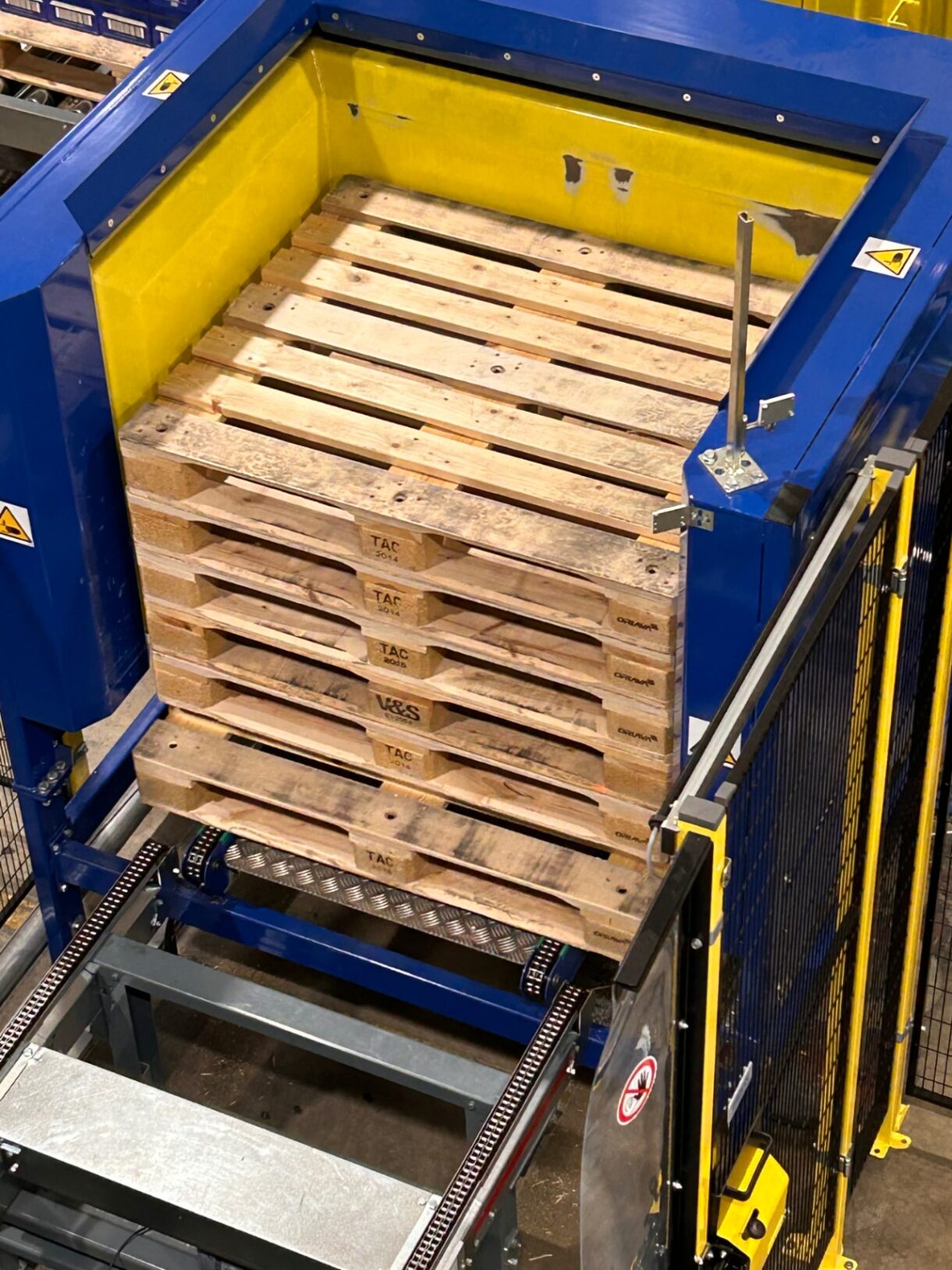
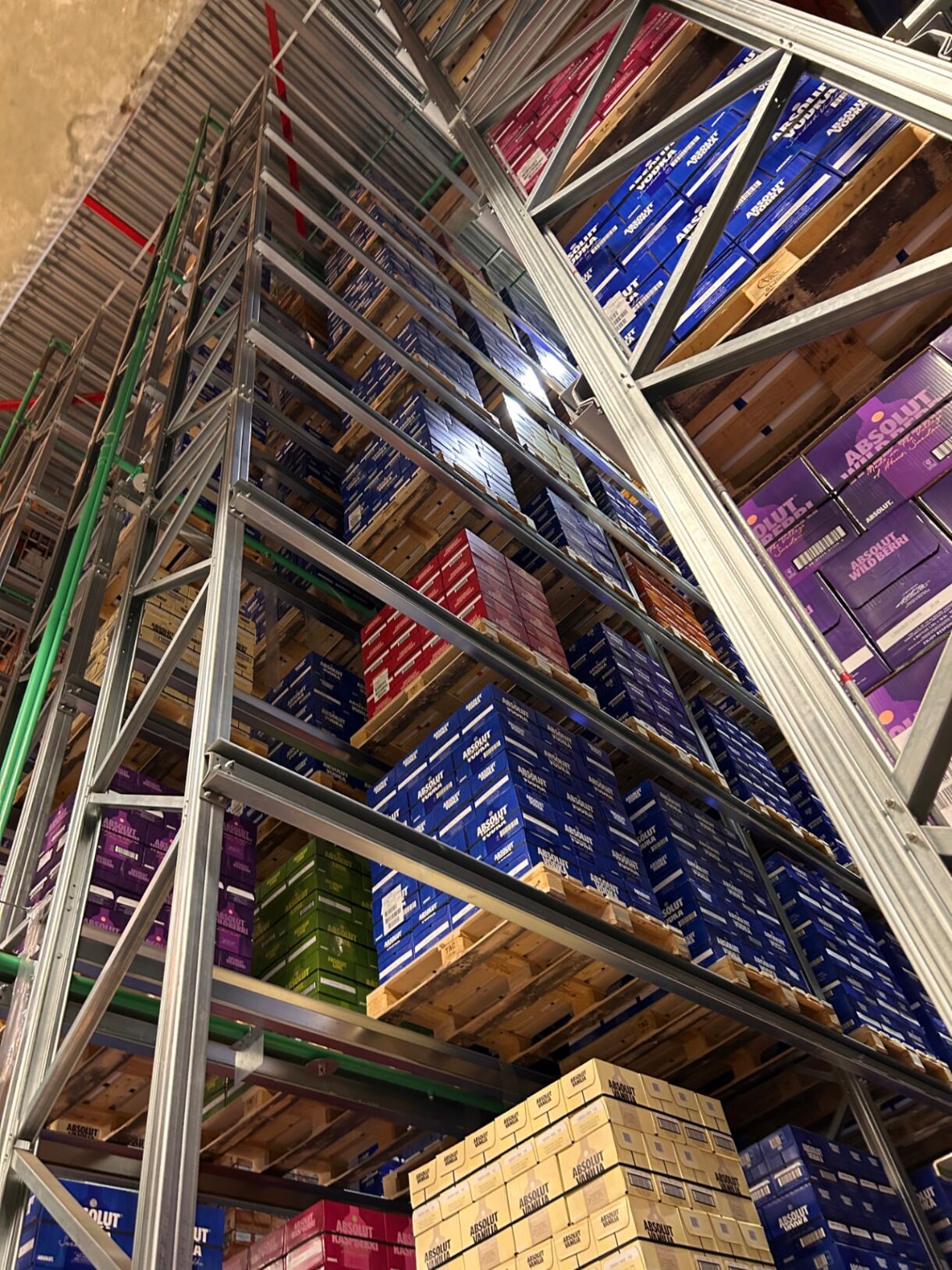
Optimisation is the buzzword
The more we can optimise the loading of shipping containers, the more we can reduce our carbon footprint. We consider three factors when it comes to improving our transportation: weight, volume, and regional rules and regulations. This year (FY23), we’ve loaded around 10,600 containers for distribution by ship and trucks. We currently utilise 88 per cent of the space in the containers we send (our goal is 94 per cent) compared to less than 80 per cent in 2010.
Our forklift drivers can modify the cargo load by adding or removing layers of cases from the pallets with a clamp truck. For example, they can stack an extra layer of cases on each pallet when loading a 40-foot container, and as a result can load 28 cases instead of 22, while still meeting the required weight. And when it comes to 20-foot containers, we typically load 21 to 24 pallets.
We save 30 cm in height in a 20-foot container by not using pallets, and this means we have room for an extra 121 cases in the container.
We have around 20,000 wooden pallets that are used internally to carry cases from our two warehouses to the loading bays (where the cases are then transferred onto standard Euro pallets for delivery). We also recycle our old internal pallets dating back to 2000 (they have our old V&S branding before we were acquired by Pernod Ricard in 2008) by selling them to Ardagh, our glass bottle manufacturer. “The pallets we use internally have a sustainably long shelf life. The last pallets we bought were in 2016,” says Harri.
But we are reducing the use of pallets all the time. We have also long adopted the use of reusable slip sheets or a blend of slip sheets and wooden pallets for ship containers, which account for 65 per cent of our shipments. We save 30 cm in height in a 20-foot container by not using pallets, and this means we have room for an extra 121 cases in the container.
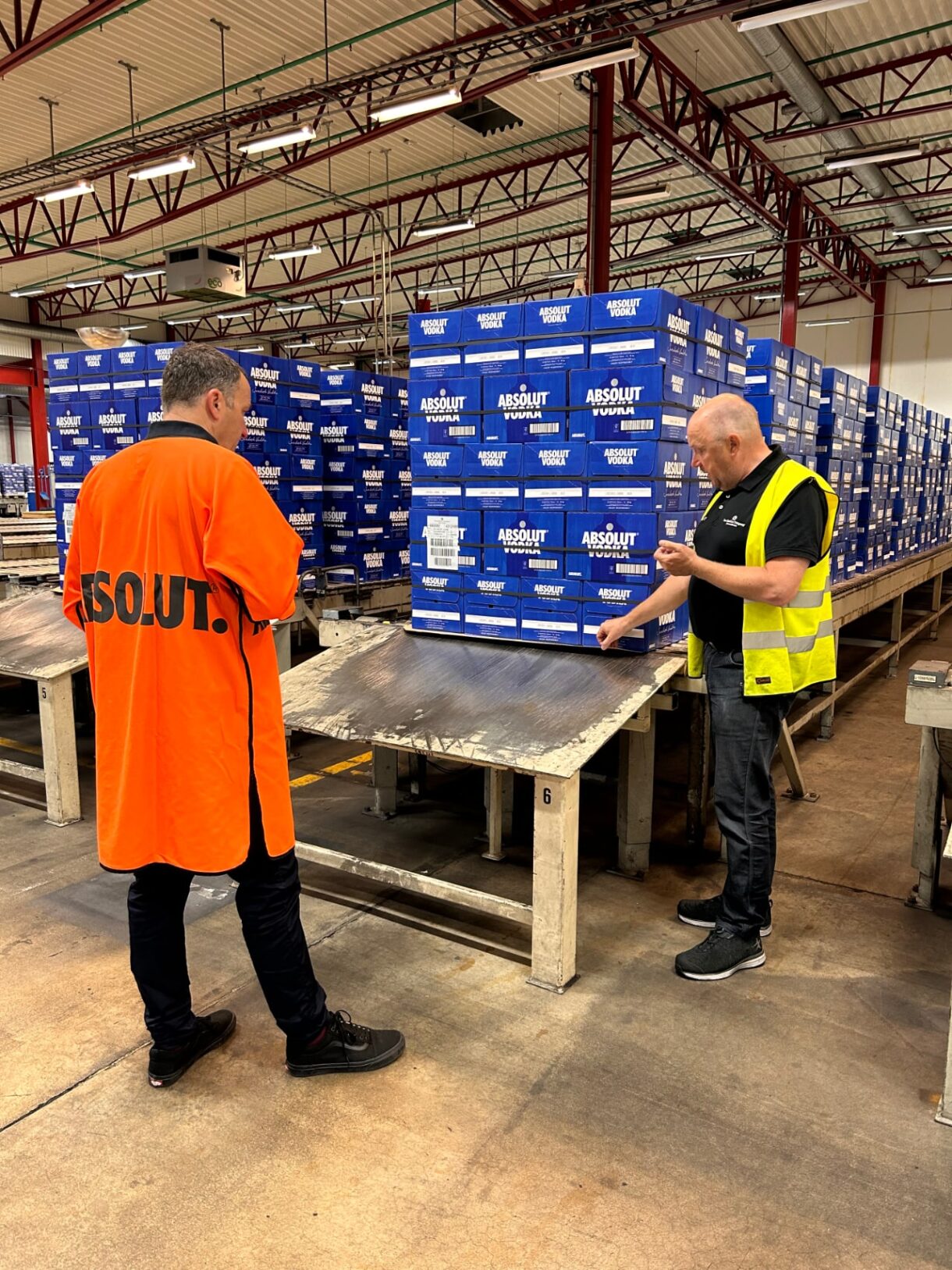
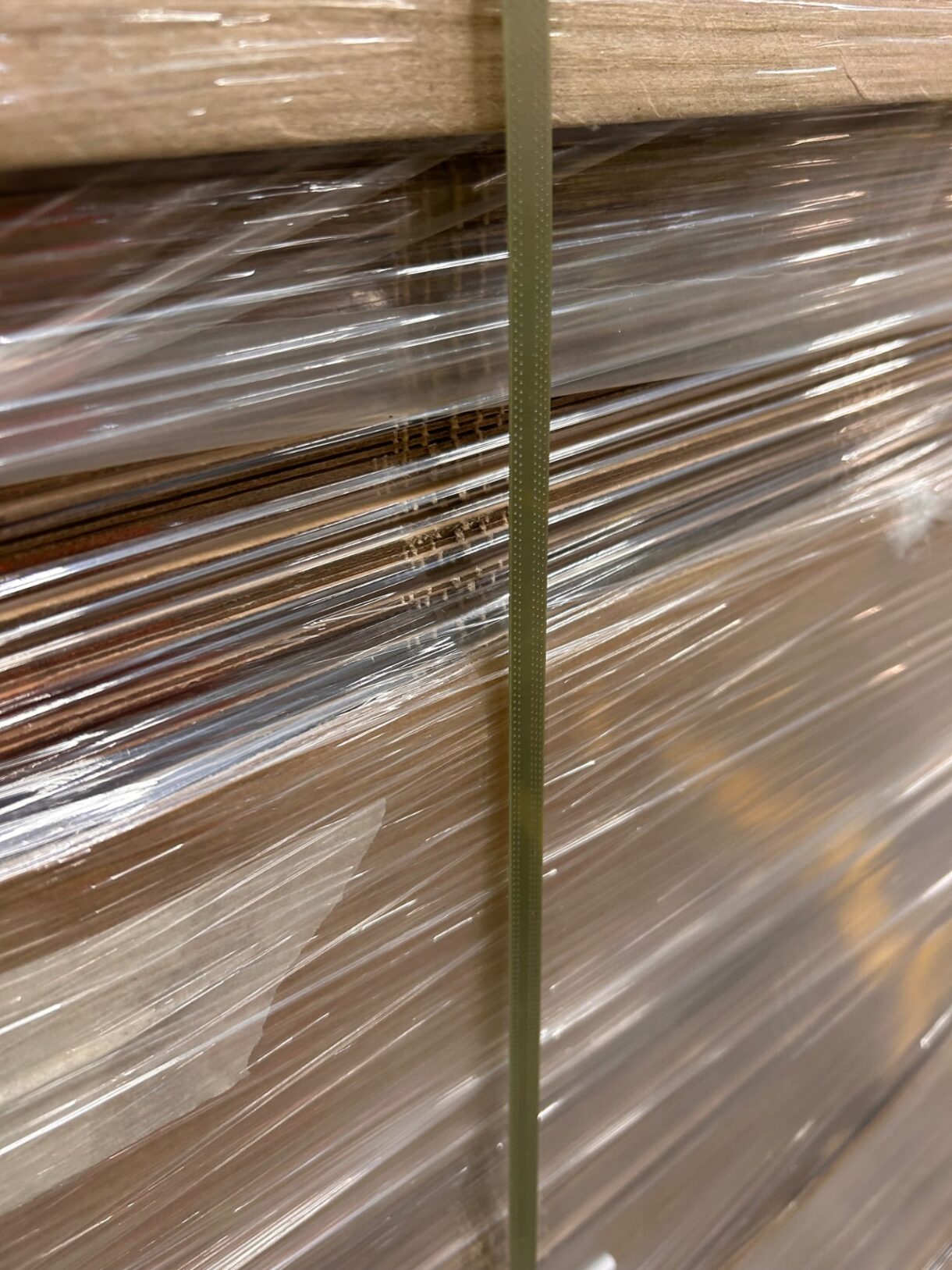
Slip sheets are made from layers of paper that are much thinner and lighter than wooden pallets. They have a tensile strength of 3000kg while only weighing 1kg – a dramatic difference compared to a standard wooden pallet with a height of 150mm and weighing 25kg.
The use of slip sheets also means less plastic. Most companies in the industry still use traditional wooden pallets when transporting products and wrap their pallets in plastic. We are currently unable to use slip sheets for truck containers (this will change next year) so we have to continue to use wooden pallets and there are restrictions on weight for road transport to consider. However, rather than wrapping them completely with stretch plastic, we use narrow plastic straps. Loading our containers in a way that doesn’t require stretch film reduces our plastic usage by approximately 45,000 kg per year.
The stretch plastic we use is made from 30 per cent recycled plastic but we are in talks with suppliers to increase this to 50 per cent.
“We only use plastic to secure cases around pallets trucks for safety and security, otherwise there will be breakages. We have no such problem with ship containers as we use slip sheets and load the pallets so tightly, they are so secure,” says Harri. “This optimisation cuts our environmental impact by 190-220 containers each year – or 4.5 million kg less cargo weight.”
The drive to optimise continues. Our goal is to increase our cargo load capacity to 94 per cent and cut the number of containers and trucks we dispatch even more. Health and safety are very important to us, and we have started an initiative called Project Layerpicker, which will help us achieve our goal.
Recycle, recycle
Recycling is a key part of the operation at the warehouse. As of last year, damaged pallets are no longer burned but instead recycled – this is an important step in our action plan to reduce the incinerated waste at all our facilities from today’s approximated 150 tonnes a year to 100 tonnes by 2025. Today it takes two weeks to fill a small combustible waste bin (see opposite) from the 16,200 sqm warehouse. “We recycle everything we possibly can, whether it’s in the kitchen or warehouse,” says Harri.
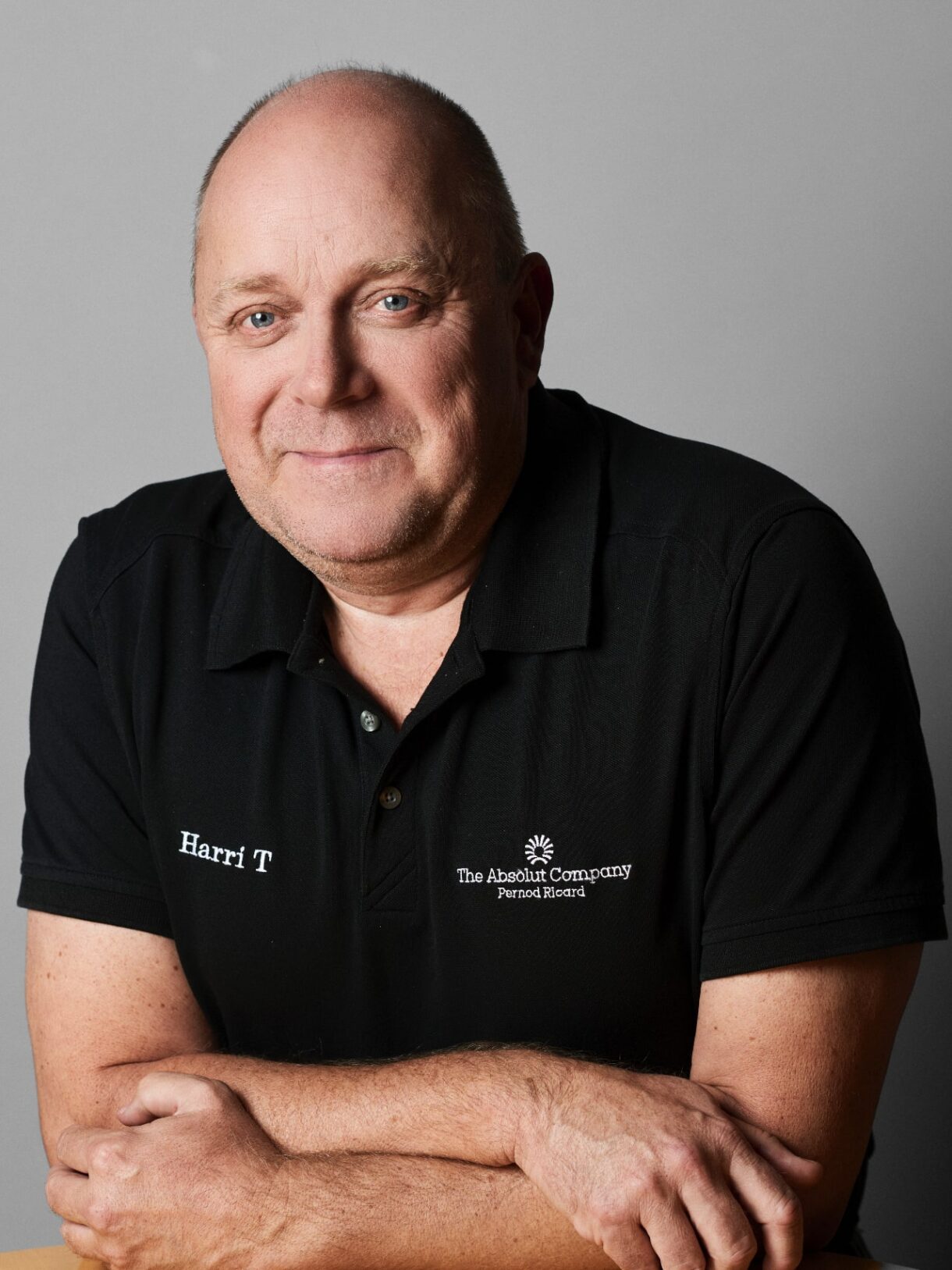