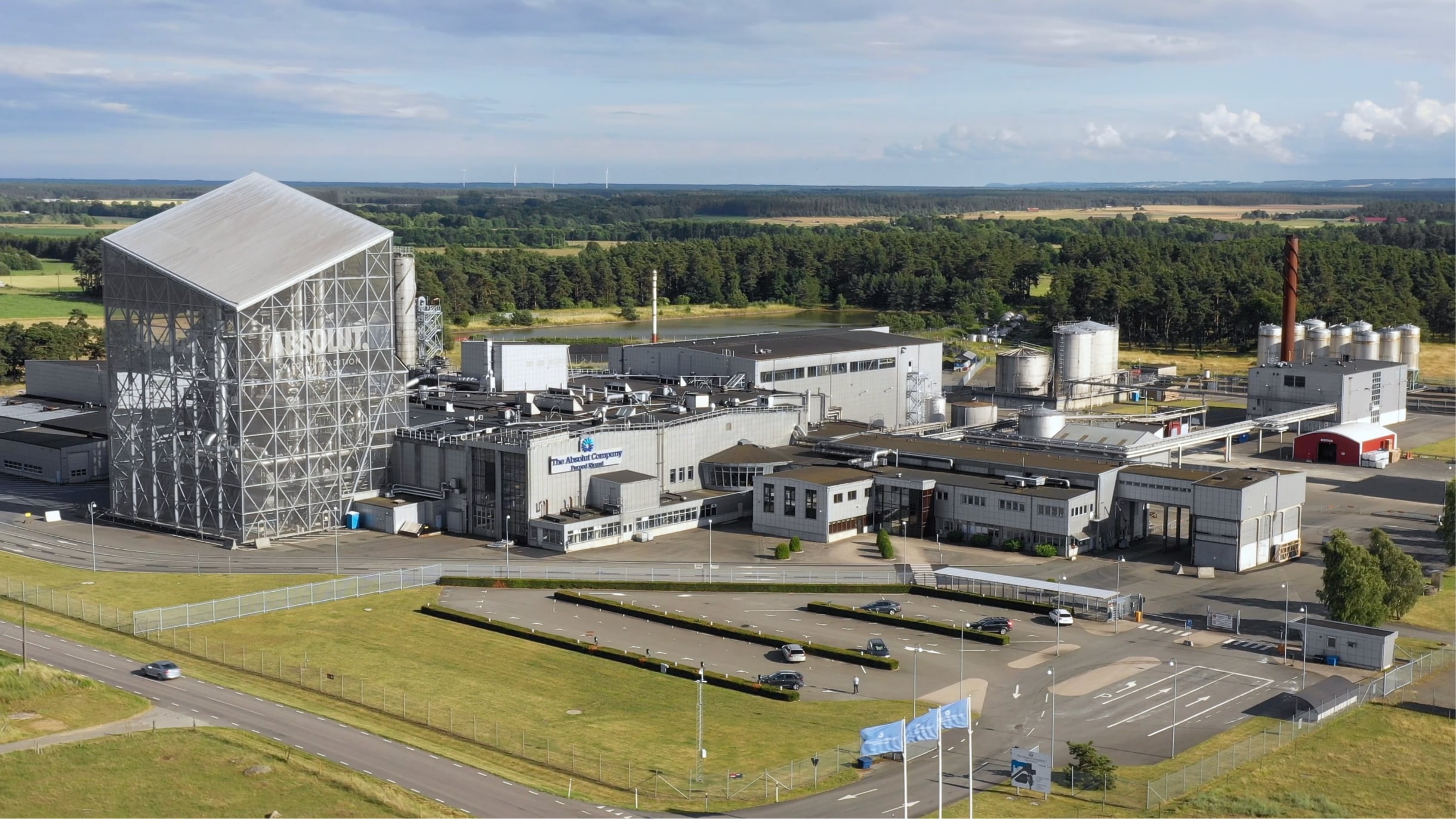
Net carbon neutral since 2013 – a fossil-free distillery by 2025
Our net-carbon neutral distillery is already one of the most energy efficient in the world – and it is closing in on another milestone by becoming fossil free.
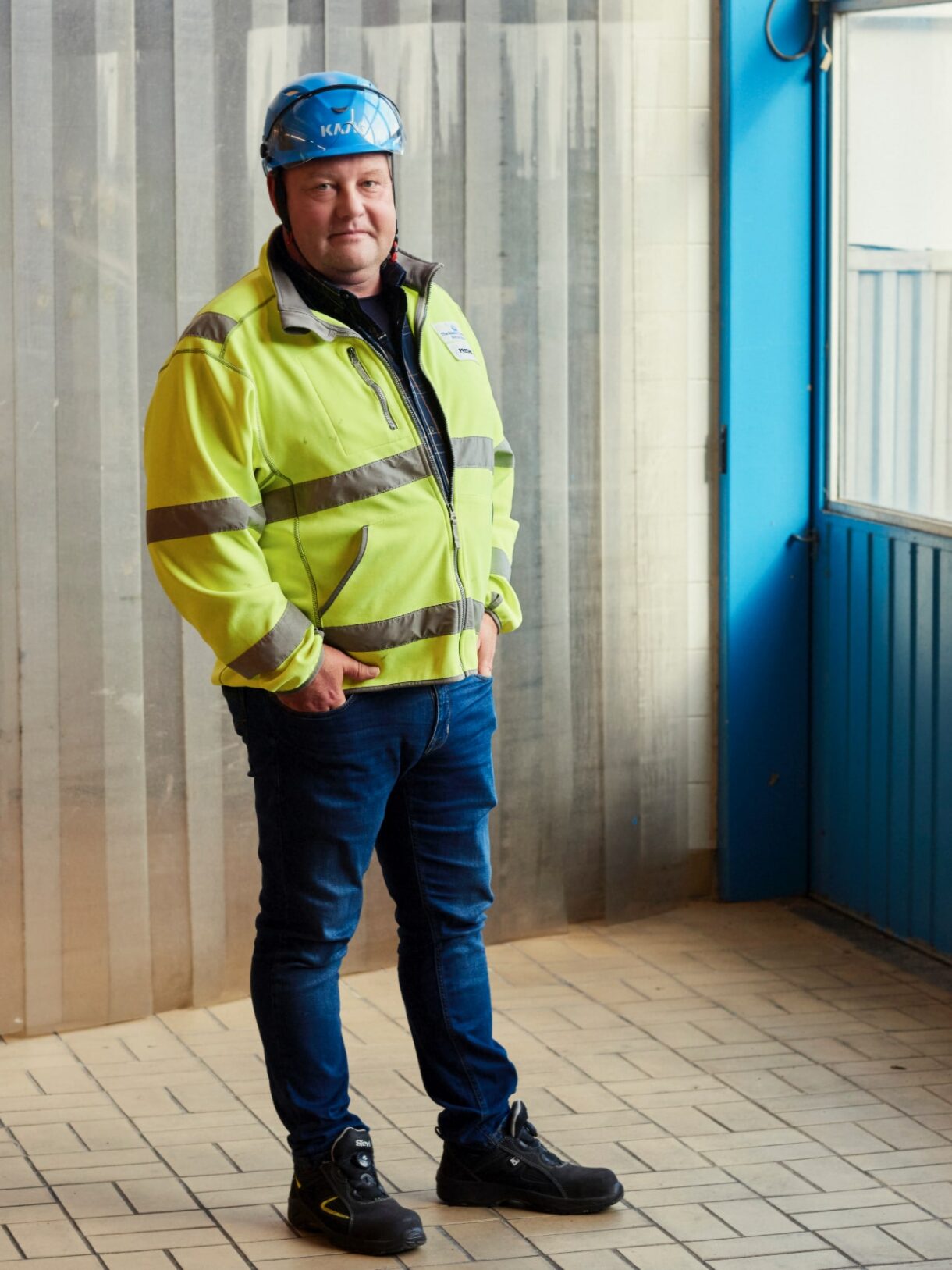
“Hocus pocus and a little bit of magic”, is the tongue-in-cheek description of our distillery in Nöbbelöv by Fredrik Åfeldt, Manager Technical Development at Absolut. But there is no trickery here. We are immensely proud that our distillery has for some time been one of the most energy efficient distilleries in the world having been net-carbon neutral since 2013. We are now closing in on another milestone with our distillery on the cusp of becoming fossil free.
“Sustainability wasn’t a word we used back in the 1980s, but we were always looking at the energy and water savings,” says Fredrik, who has seen the progress first hand having joined Absolut straight from university in 1986. “We have designed our distillery’s technology to get the best out of the process and deliver the best quality product. We have chosen to run it on low pressure. It has been built like a giant piano, with different keys – we can run the distillery in different ways depending on demand to remain efficient.”
A new distillery was built in 2004 with seven 25-metre-high spirit columns – a mash column, a spirit column, an extraction column, two rectification columns, a methanol column and the recovery column. Since its installation, the energy consumption in all our facilities per litre of vodka has decreased radically by 40 per cent and the distillery is close to being fossil-free.
Today, 80 per cent of the energy used at the distillery comes from green electricity, around seven per cent from green fuel (made in-house using waste spirits) and the remaining 13 per cent is generated using LPG. We are now phasing out the LPG that makes up the remainder of the fossil power with biogas by 2025. “We are 100 per cent on track,” Fredrik says. “Our backup distillery facility, which is used when demand is particularly high, will be fossil-free by 2025 too.”
We are immensely proud that our distillery has for some time been one of the most energy efficient distilleries in the world having been net-carbon neutral since 2013. We are now closing in on another milestone with our distillery on the cusp of becoming fossil free.
Waste is a word to be scorned for us here at Absolut. We use discarded spirits in a resourceful and circular way at our distillery and we recycle or reuse everything at our facilities with zero production waste going to landfill.
Within the distillery, we have invested in a facility that is dedicated to distilling waste spirits, which include discarded flavoured vodkas from defective bottles or discontinued products, to turn it into fuel.
Waste spirits from bottling are distilled into ethanol and water. Since the outset, we have distilled 1 200 000 litres of these waste spirits and generated 400 000 litres of ethanol. The ethanol is combined with two other streams of unwanted substances, such as propanol, from the main distillation at Nöbbelöv and used to replace LPG to fuel the distillery. In this way we can generate around 25 per cent of the distillery’s steam power.
During the past year we have installed a ‘fusel oil wash’ to clean and separate water from the fusel oil (a waste stream of the alcoholic fermentation process). By reducing the water content of the fusel oil to less than 10 per cent, we can use this too as a source of energy.
“When it comes to vodka there is a lot of water in it, so much of it can’t be used as fuel (it can only burn if it contains less than 10 per cent water), so we are extracting the water so we can upgrade the discarded vodka as fuel, combined with other waste streams from our distillation” says Fredrik. “This internally produced fuel is now a certified sustainable biofuel and used as energy for our distillery.”
The largest by-product left over from the mash process (where the wheat is mixed with water and enzymes for the fermentation process) is stillage. Referred to as ‘drank’ in Swedish, it is high in protein and makes a good animal feed and it is fed to around a quarter of a million pigs and cattle in the south of Sweden each day.
Our 45-strong team working 24/7 at the distillery continue to unpick the distillation process and continue to rework their operations to squeeze every ounce of efficiency with a focus on greater sustainability. “Every time we do some investments, we get better,” says Fredrik. “We continue to update our systems and optimise to get even better.”
The Absolut distillery
We invested in a new spirits distillation plant that was put into operation in 1996 with the main goal of increasing the amount of vodka we could produce without increasing our energy consumption. The new distillery went further and after just four years we had reduced its energy consumption by half.
In 2004, we opened an entirely new distillery in Nöbbelöv, this time with the specific purpose to reduce energy consumption even further. Within four years, we had reduced our energy consumption by half again. Our distillery is now considered one of the world’s most energy efficient.* Adding to that the fact that more than 85 per cent of the energy we use at our production sites comes from renewable sources, explains why our distillery emits more than 90 per cent less carbon dioxide per litre distilled spirits than the average distillery*.
* According to Beverage Industries Environmental Roundtable (BIER) benchmarking study based on data from 2020 our distillery used 69% less energy and emits 98% less CO2 per litre of distilled spirits than the average distillery.