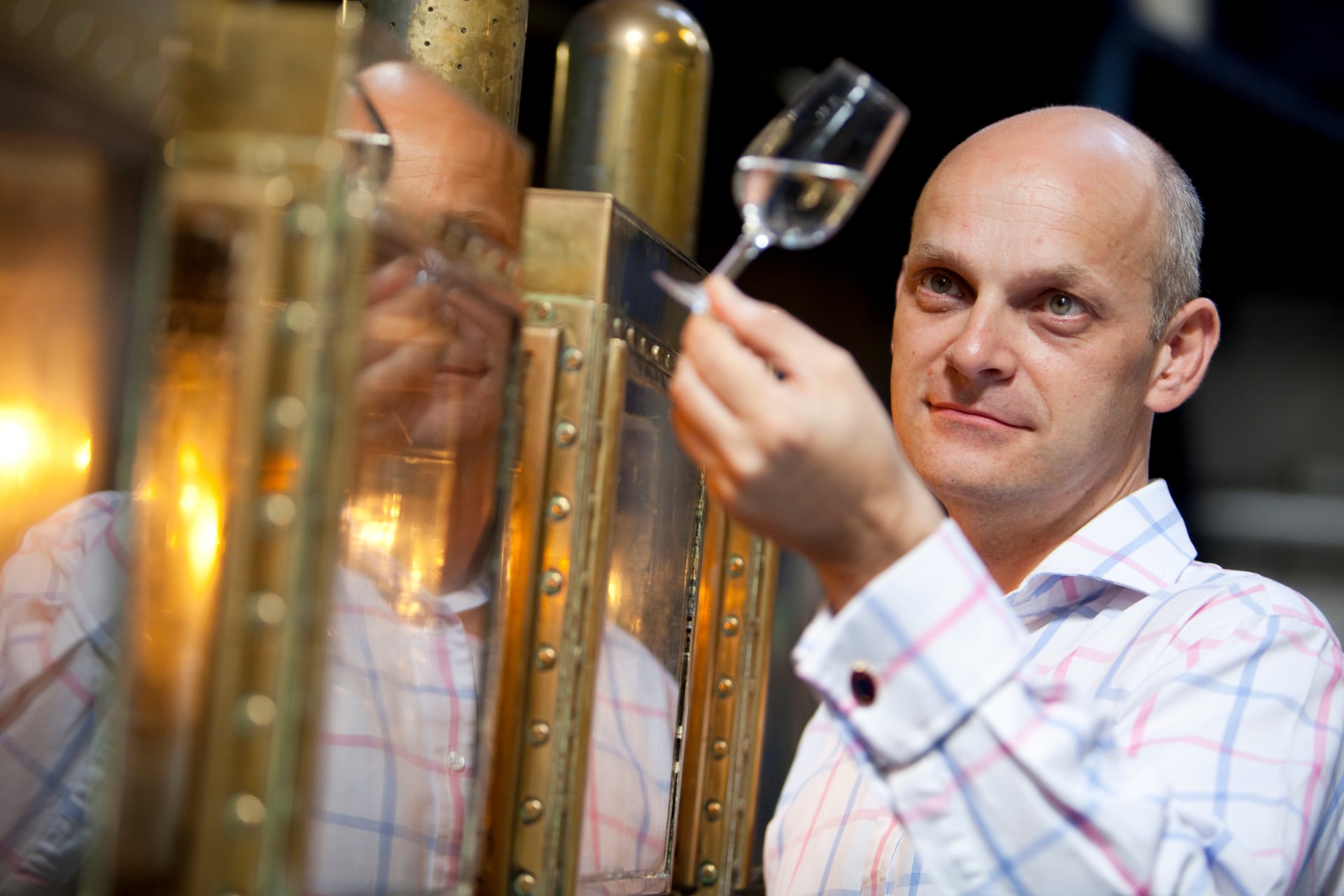
Plymouth Gin reaches fossil-free milestone
Plymouth Gin has implemented several initiatives in recent years to reduce its carbon footprint but the arrival of electric boilers in 2024 means that production at its historic distillery is now fossil-free.
We have been making Plymouth Gin at the Blackfriars distillery, the oldest working distillery in England, since 1793. Based on the coast in the historical town of Plymouth in southwestern England, our gin is still hand-crafted and batch-distilled, using the soft water from the rivers of neighbouring Dartmoor.
“The oldest part of the distillery is five centuries old, the newest part around 70 years old. This means that we need to adapt a historic building to make our operations more sustainable,” says Sean Harrison, Master Distiller at Plymouth Gin. “We’re too small a brand to change the world. We have just been keeping an eye on technology and have implemented changes as we go. Simple things like changing all our light bulbs from fluorescent to LED saves a huge amount of power and money very quickly, for instance.”
Besides being fossil-free our electric boiler only takes 20 minutes to be operational from the moment you press the button.
We have taken some significant steps to reduce our footprint. While the distillery may date back centuries, its operations are powered by 100 per cent renewable electricity. We recycle all waste botanicals via an anaerobic digestion power plant to turn the waste into renewable energy. Today, our distillery can claim to be fossil-free having built a new boiler house and replacing our natural gas-run still and domestic boilers with electric boilers in 2023.
“Over the past few years, we’ve constantly looked to lower our footprint as much as technology has allowed us to. We don’t send any waste to landfill – it is either recycled or incinerated. Our waste botanicals are decomposed at a biogas plant creating methane gas which is then used by power plants,” says Sean. “The installation of the electric boilers is a terrific milestone to have reached so soon. Besides being fossil-free, our electric boiler takes 20 minutes to be operational from the moment you turn the button on. The old gas boiler used to take a good hour to get up and running. An electric boiler is much safer to use too!”
Other initiatives, such as with packaging, are also making a difference. Dividers have been removed from cases, while three years ago, we made our distinctively shaped glass bottles 15 per cent lighter (saving around 60 tonnes of carbon a year). The iconic monk logo that sits at the bottom of the bottle, which used to be applied as a plastic label is now elegantly embossed directly onto the glass. At the same time, we removed all single-use plastic, introducing paper labels and an updated cap from PVC to recyclable PET.
“I find it strange that many people think that the heavier something is the better it has to be,” says Sean. “So, when people pick up a bottle that isn’t very heavy, they think the quality of its contents is poor. This misperception needs to change because making bottles lighter is one of the quickest ways to save energy – and quality doesn’t have to suffer.”
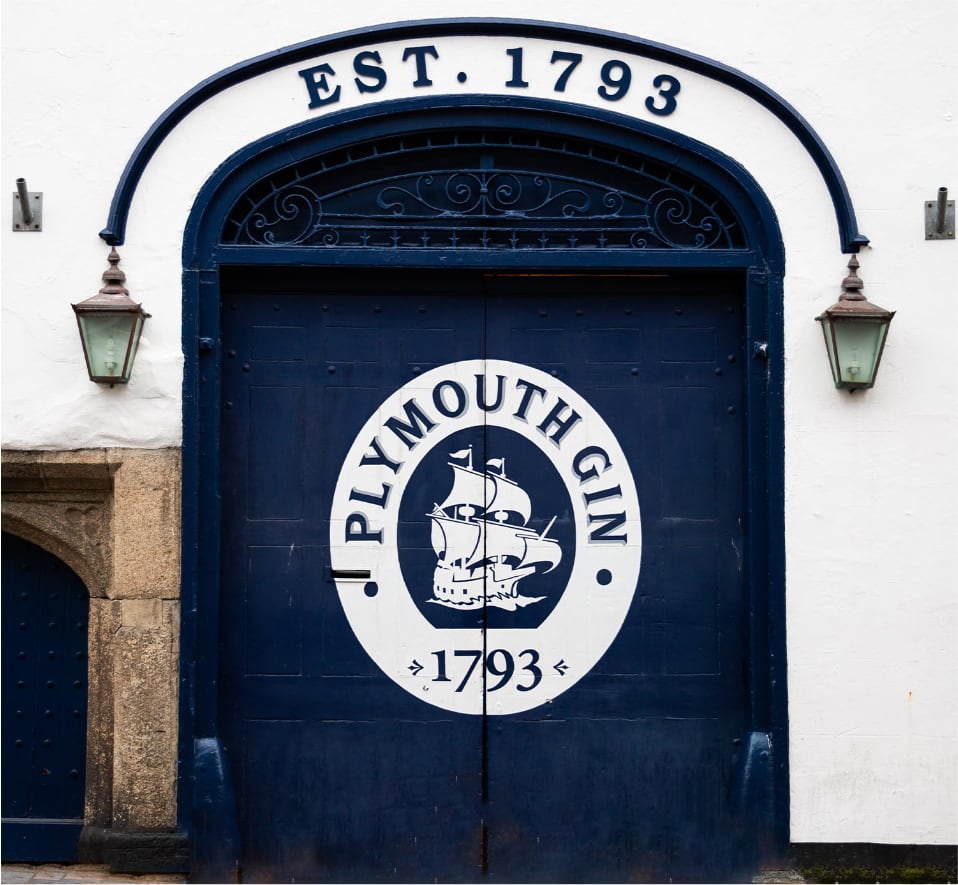
A distillery with a 500-year habit
The distillery buildings that date back to the 1400s were formerly a monastery inhabited by the Black Friars and Plymouth’s location by the sea made it a convenient meeting point for 17th-century pilgrims boarding the Mayflower. The Pilgrim Fathers even spent their last night in the distillery before they set sail on the Mayflower on their epic voyage to start a new life in America. We continue to pay homage to this association with an image of the Mayflower on every bottle.