The supply chain reaction
The procurement process is at the core of our sustainability work, whether it’s sourcing energy supplies, handling products or logistics – and a single change can have positive ramifications along the supply chain.
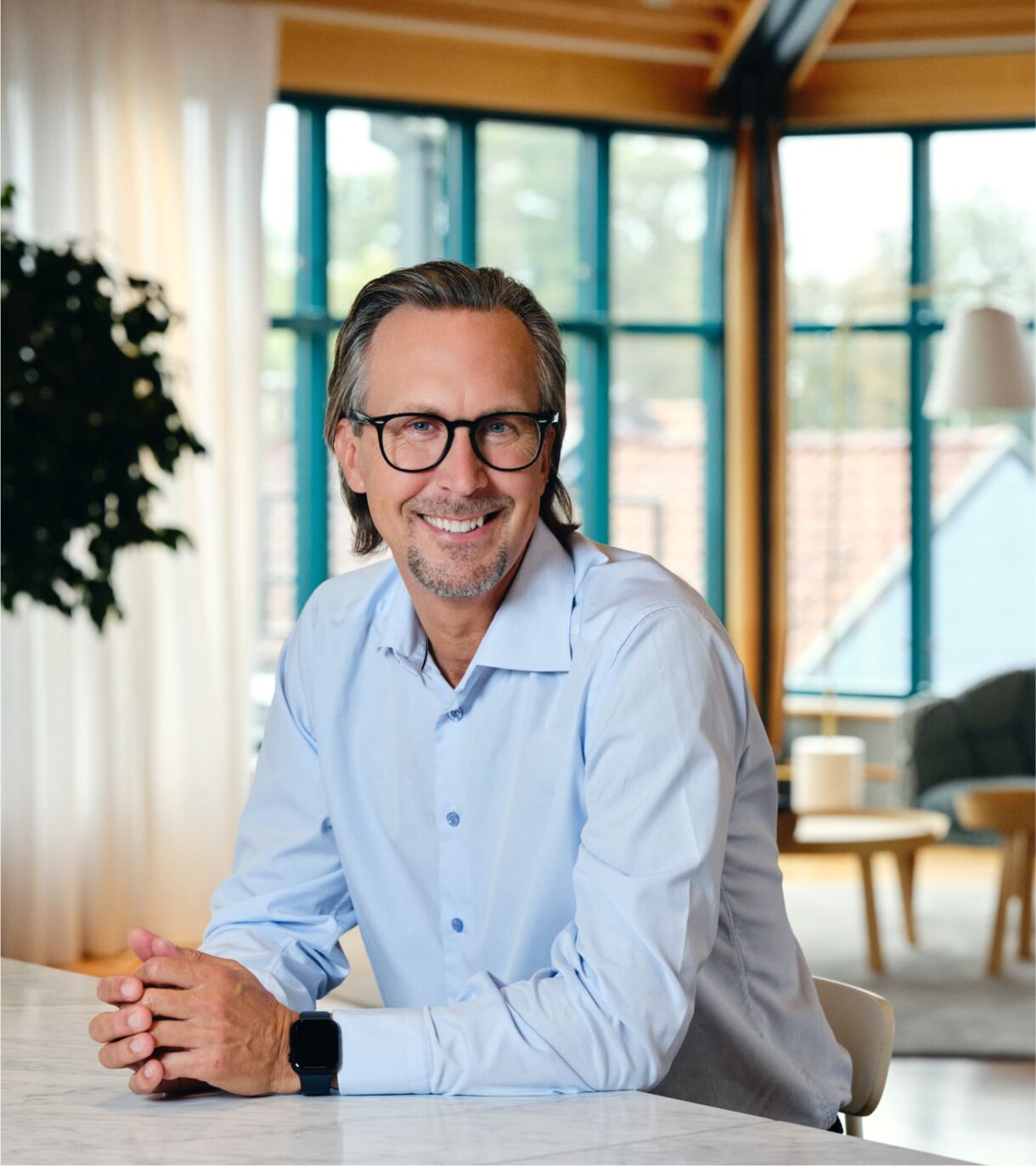
Sustainability is part and parcel of what we do in procurement. We are constantly searching for ways to improve; whether it’s minimising CO2 emissions from transport, choosing renewable energy, sustainably cultivated wheat or packaging with a lower environmental footprint.
“We are digging into every single detail, just to make it more efficient and better for the environment. We plan at least 10 years ahead and work very closely with all our suppliers to ensure we can fuel our growth,” says Johan Blixt, Procurement & Supply Chain Director, The Absolut Group. “It is symptomatic of procurement to focus on costs but today this goes hand-in-hand with sustainability and trying to do things better for the environment. At least if you want to be around in the long run.”
We have long had regular meetings with all major suppliers to propose and investigate potential value creation projects. All projects are important to be able to optimise our footprint.
Our initiatives can impact the entire supply chain. Take our glass bottle, for example. We have already made strides in making our iconic glass bottle lighter. In 2015, we reduced the weight by 10 per cent while retaining the bottle’s iconic shape and strength. This, in turn, reduced the CO2 emissions in the production of the bottles but also on transport (and the costs) because you can transport more bottles per container. It also means fewer pallets are needed. “As there is a fixed cost handling every pallet that’s a cost we can reduce as well,” adds Johan.
We recently removed the vast majority of dividers in the shipper cases for Absolut Original without adding more scuffing to the decoration. The impact on internal handling, sustainability and cost is significant. This is not just the case for Absolut but for the companies at the other end of the supply chain receiving the pallets. Likewise, we recently removed the protective dividers in boxes for all flavoured vodka bottles from the supplier to our plant. This has reduced the number of pallets we use by 43 per cent and reduced transport by 23 per cent, reducing 78 tonnes CO2 emissions and 200 tons of waste material.
“It is like a domino effect,” says Johan. “If you have 8,500 fewer pallets to handle in production, fewer forklifts are needed while it removes 200 tonnes of material that needs to be handled or recycled.”
It is like a domino effect. If you have 8,500 fewer pallets to handle in production, fewer forklifts are needed while it removes 200 tonnes of material that needs to be handled or recycled.
Johan Blixt, Director Supply Chain
For some time now, transport between the distillery, the bottling plants and the warehouse has been fossil-free, mainly by using HVO instead of diesel. “For transport from the bottling plants to the warehouse, we have funded and co-invested with our transport supplier to use electric trucks,” adds Johan. “We also work with our material and wheat suppliers to increase the percentage of renewable fuels in all deliveries.”
We collaborate with our partners across our full supply chain, although the biggest challenge is with the shipping companies. Despite being a global brand, it can be a challenge for us to influence shipping lines into implementing more sustainable solutions. The ships that we load our containers on can hold up to 25,000 TEUS (20 containers) – not even our yearly volume is big enough to fill up a ship of that size.
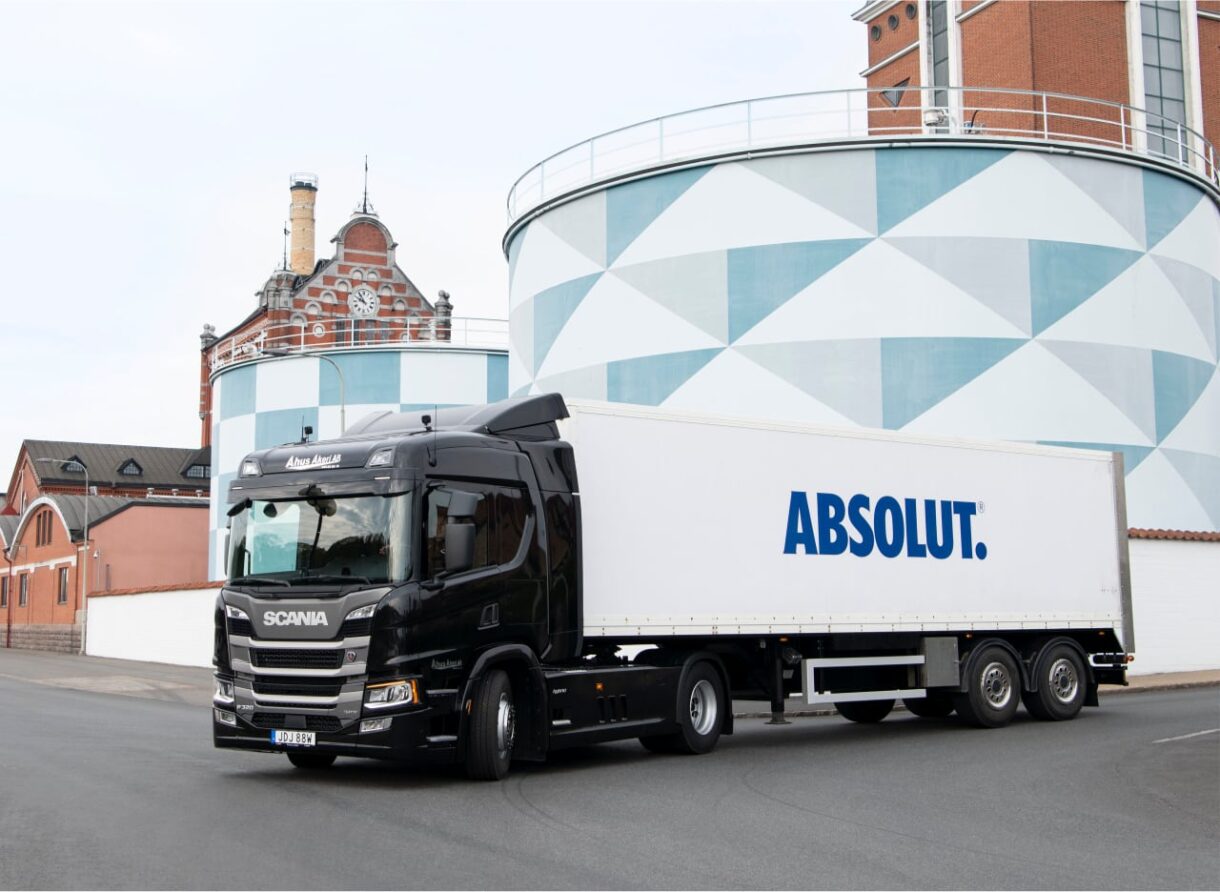
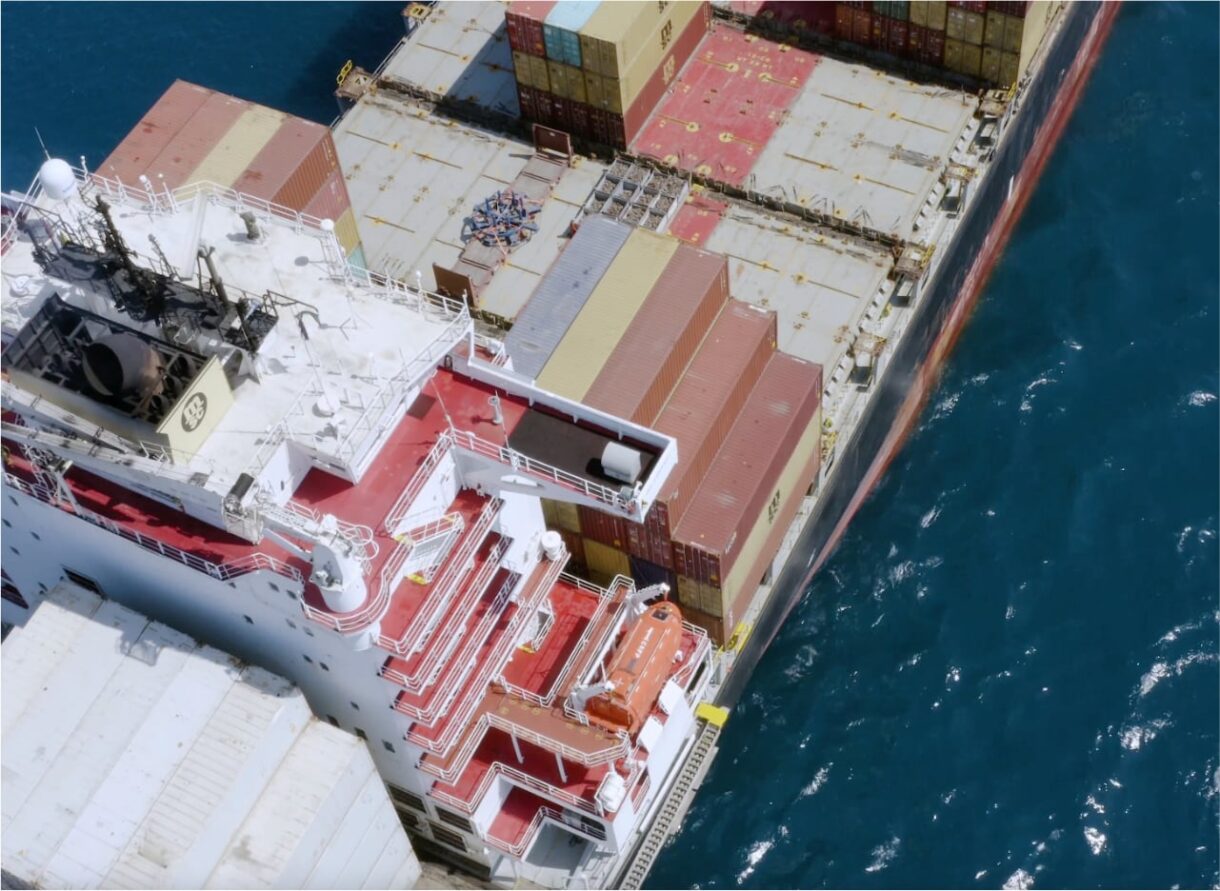
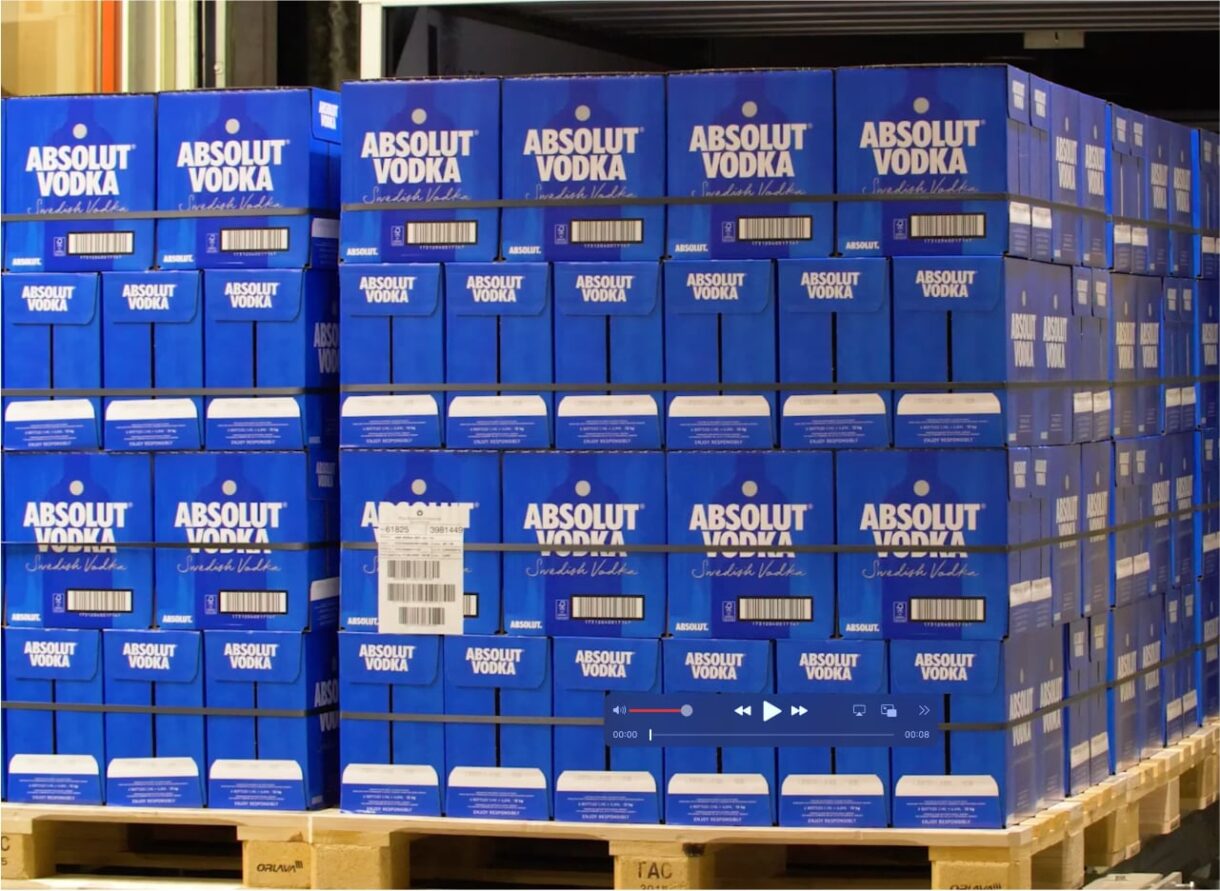