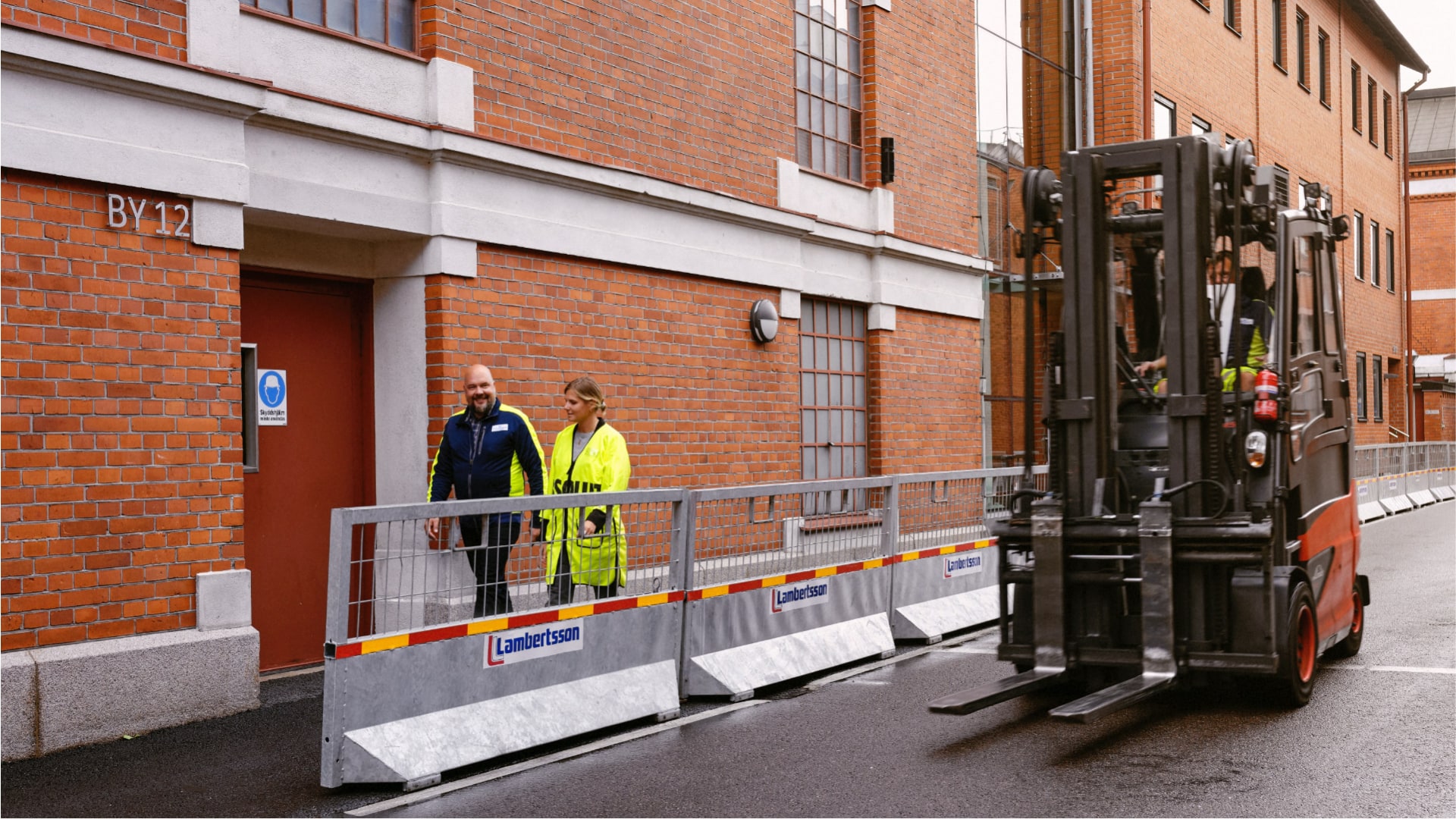
Breaking down the safety barriers
Our ambition is to become ‘best in class’ across the wine and spirits industry when it comes to Health and Safety.
We are working hard to reinforce H&S training across the company, from operators to managers to safety representatives. Not only does the training programme emphasise the rules and procedures around safety, but it is also designed to change the attitude of employees, so we become a safety-first-culture workplace.
Changing behaviours requires awareness, knowledge and strong leadership. During 2022 we developed a three-year Health and Safety roadmap, which is broken down into action plans, training programs, audits and targets – and a new Health & Safety (H&S) manager who is driving the initiatives.
The new manager, Dainius Januskevicius has strong attention on Lost Time Accidents (LTAs) which is a measure of safety standards. In the Pernod Ricard Group we have a vision of zero LTAs by 2025, but for Dainius, while targets are important, his main objective is to create a culture of safety, where health and safety become second nature to employees. A favourite anecdote of his is the story of the Cobra effect, which describes how an attempted solution to a risk can make the problem worse, and why numbers do not tell the whole story.
The key is to minimise the risks in the first place and minimise the seriousness of them.
Dainius Januskevicius, Health & Safety Manager
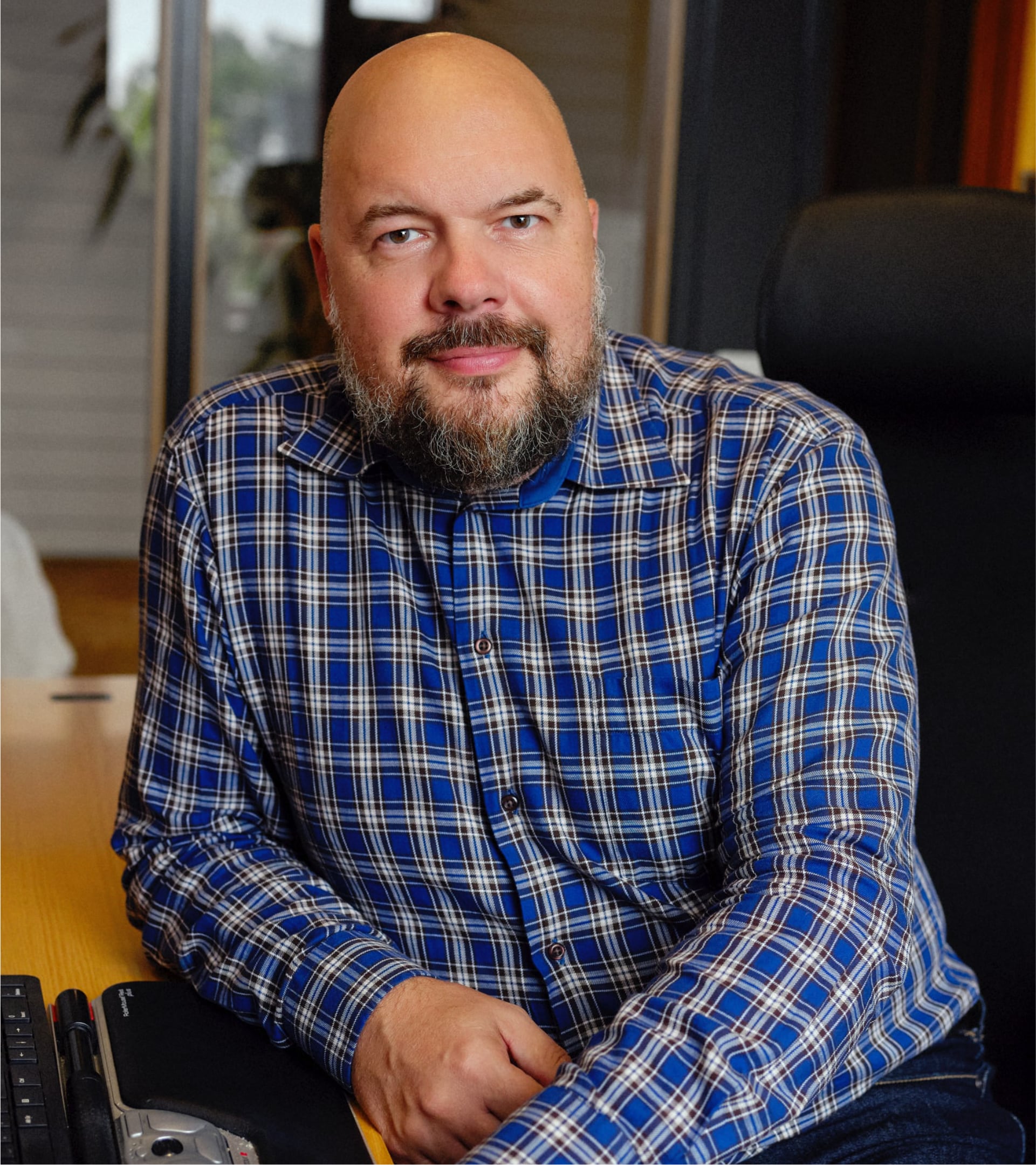
Learning from the Cobra effect
The story goes that during British colonial rule in India, there were too many venomous cobras in Delhi. To reduce the cobra population, the British government offered a bounty for every dead cobra brought to them. Initially, this seemed like a reasonable solution, as it incentivised people to kill cobras and collect the reward. However, the unintended consequence was that people began breeding cobras to collect more bounties. As a result, the cobra population actually increased rather than decreased.
“The beauty of this cobra anecdote is that it shows that statistics can be misleading because the strategy did not minimise the risks – and it’s the same with health and safety,” says Dainius. “Safety reports don’t tell the whole story or the pain from injury. You can have a vision and a solid plan on how to minimise the risks, but accidents will happen. The key is to minimise the risks in the first place and minimise the seriousness of them.”
At the heart of our Health and Safety strategy is the Care By Learning programme which follows three golden rules: for everyone to look out for one another; to stay focused on the task at hand: and to take personal responsibility. Some 200 employees have already undertaken half-day intensive workshops as part of the programme that includes theory and practice. Nominated trained Safety Champions are given extra training and embark on care visits to support and reinforce the training on the shop floor.
Changing our mindset
We use the renowned Bradley Curve, which illustrates the relationship between accidents and corporate culture. By looking at key behaviours and mindsets, we can progress and follow our improvement on the curve. Our maturity level is increasing, which shows that our co-workers are beginning to think independently about health and safety.
“We’re going to the shop floor; we’re introducing ourselves to co-workers and saying it’s important to talk about the safety. The impact is already noticeable. Workers are starting to take action, they understand risks and reporting more potential safety hazards,” says Dainius.
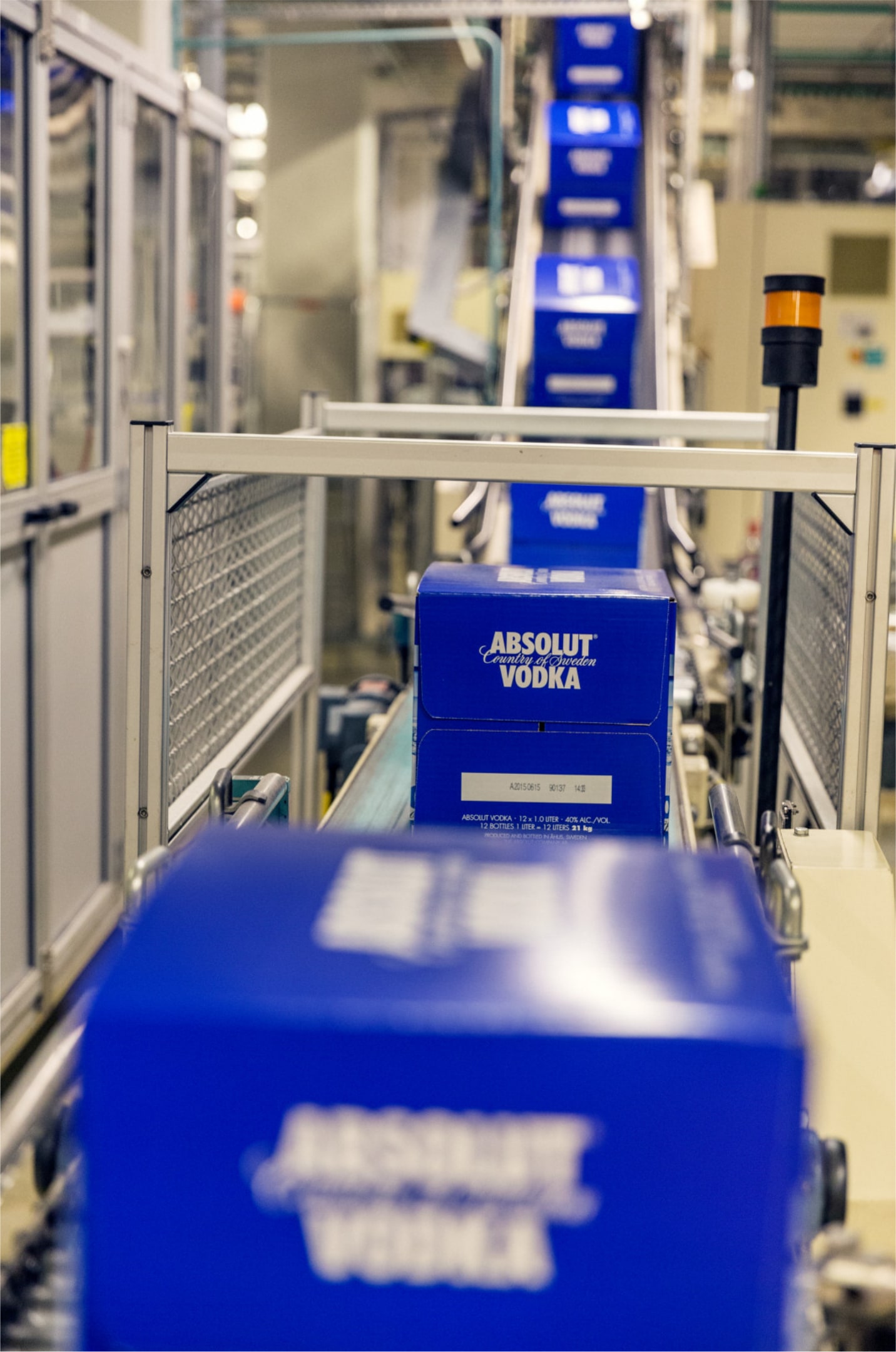
We have separated the areas with a barrier, whereby previously they were just floor markings. Now, the forklift doesn’t need to go at the lower speed because there is no longer co-activity area.
Dainius Januskevicius, Health & Safety Manager
During last year, we have really improved safety features in the warehouse and other areas where we have pedestrian and forklift co-activity areas. For example, in line with Pernod Ricard Operational Regulations, speed restrictions should be in place for forklifts, where co-workers are walking. However, we undertook a risk assessment that has resulted in barriers being put in place to fence off pedestrian areas.
“This is the key to safety. It’s not necessarily about the speed restrictions, which even at a lower speed could seriously injure a worker. We have separated the areas with a barrier, whereby previously they were just floor markings. Now, the forklift doesn’t need to go at the lower speed because there is no longer co-activity area. At the same time, pedestrian co-workers feel much safer because they are separated,” says Dainius. “There is no risk.”
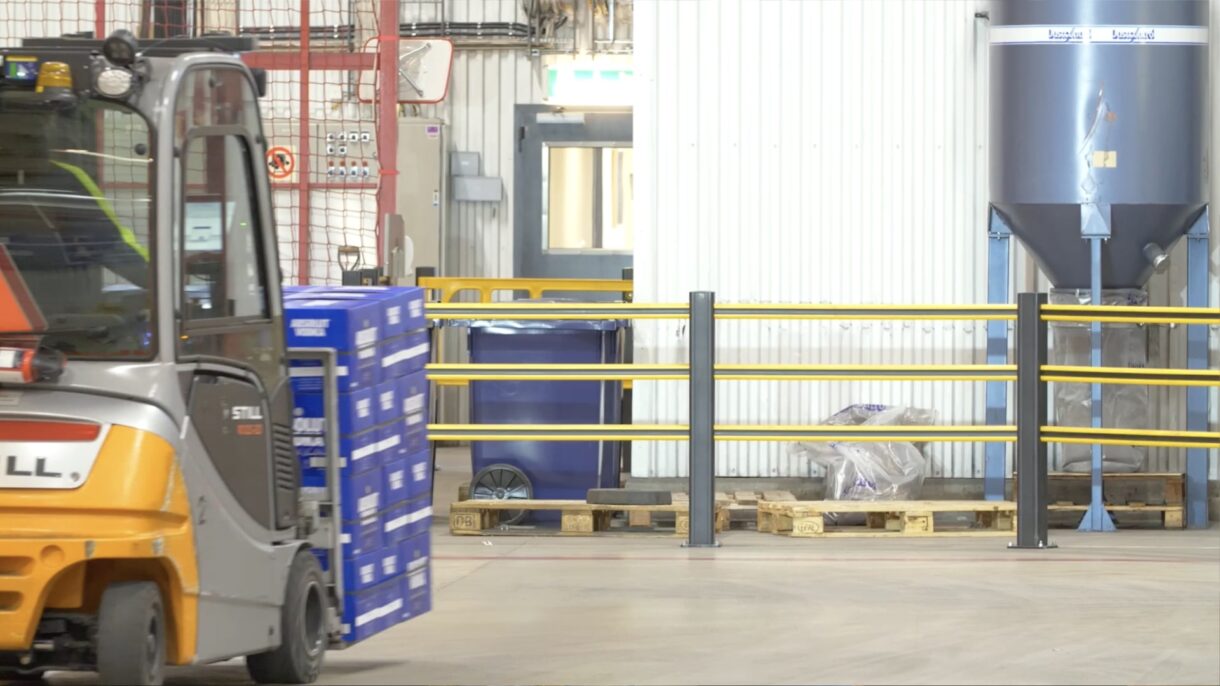
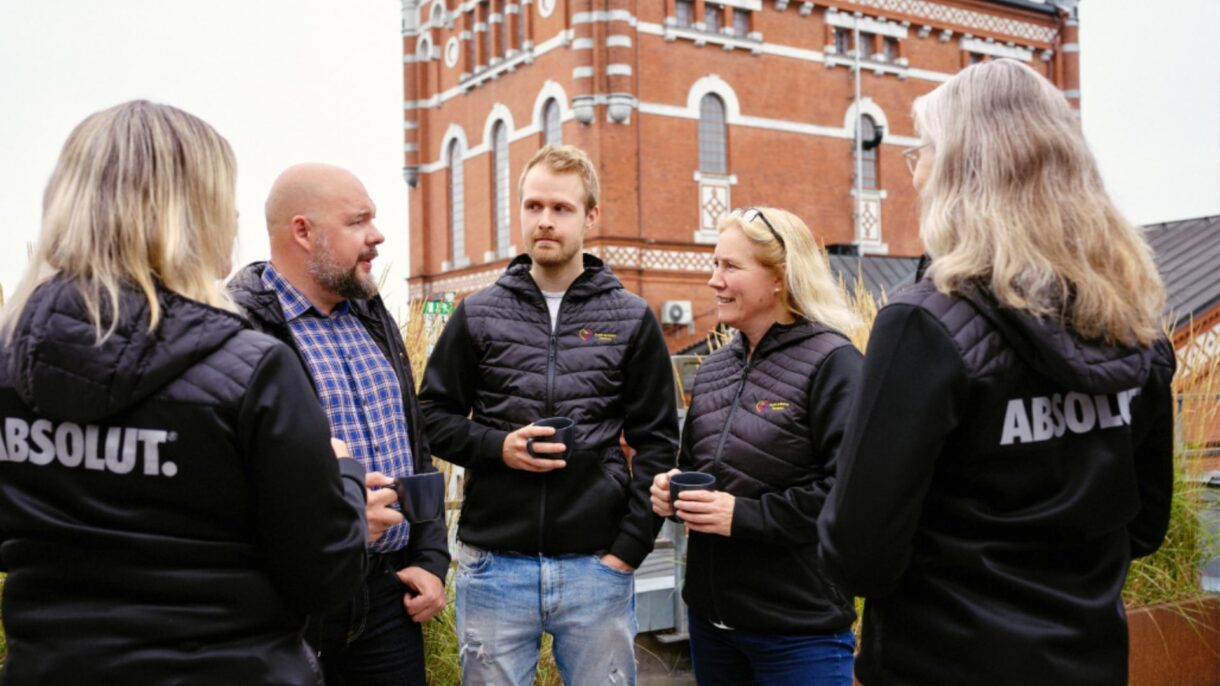