Absolut carbon roadmap: On track as normality returns
A core part of our sustainability strategy is a commitment to make Absolut Vodka a carbon-neutral product by 2030.
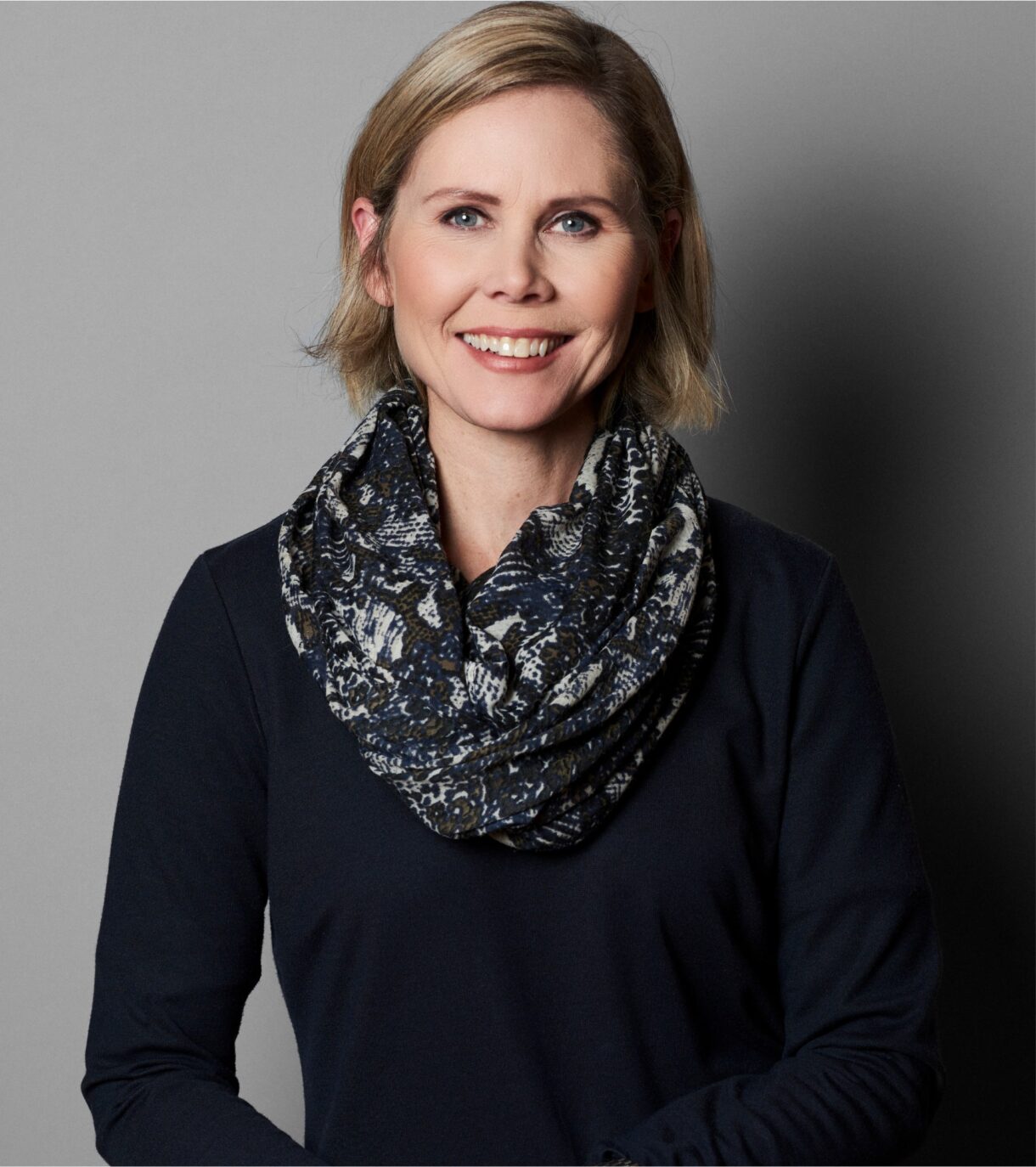
We began the year as it had ended when a record 13.6 million cases had been produced. Demand remained buoyant and despite continued global supply chain disruption, our long-term partnership with suppliers held us in good stead. We were able to handle increased shipments and deliver to our customers without any disruption. By the end of FY23, production had begun to return to pre-pandemic levels and there was an overriding sense that normality had returned.
“It was an overwhelming start to the year as demand remained very high. But we had learned a great deal from FY22’s unplanned record production, by adding in more regular shifts and keeping seasonal workers on after the summer,” says Anna Schreil, VP of Operations, The Absolut Company. “This year’s spring volumes, which in the past were less than autumn’s, have normalised. This has allowed us to catch up on face-to-face health and safety training, which we hadn’t been able to do because of restrictions and shut down production lines to carry out routine maintenance too.”
Normality returns as emissions fall
The return to more predictable levels of demand for Absolut Vodka and stillage in FY23 resulted in Scope 1 & 2 emissions falling to 1985 tonnes* as we did not need to use the backup facility as much. The resulting carbon efficiency of our distillery and bottling was 17 g CO2/l vodka compared to the previous year’s 34 g CO2/l vodka. This was a welcome reduction from FY22 when we had reopened our backup facility (which, given its age, is not as carbon efficient as our main distillery) to meet unprecedented demand.
Also, drying the stillage led to increased emissions levels in FY22. Our main by-product of the distillation process, wet stillage, is sold to local farmers as feed for pigs and cows. The unexpected increase in demand for vodka in FY22 meant we had far more stillage than the farmers had planned for, or indeed needed. Subsequently, this impacted our overall emissions score, as to store the stillage we had to dry it first (losing 90 per cent of the wet stillage that is water) at our drying plant facility using fossil fuels. However, by the end of FY23 we had found a strategy to reduce the need to dry the stillage.
“The main driver of excessive energy and fuel consumption in FY22 was the fact we had to dry stillage. Stillage is great fodder, but we didn’t plan for so much more spirit to be produced, nor so much stillage to be generated– you cannot feed pigs more than they need and so we couldn’t sell all our stillage,” says Anna. “However, despite consuming a lot of energy, dried stillage is still great fodder and has value and was later also sold.”
I love efficiency, I love circularity and despise waste. I want to work smarter, not harder.
Anna Schreil, VP of Operations
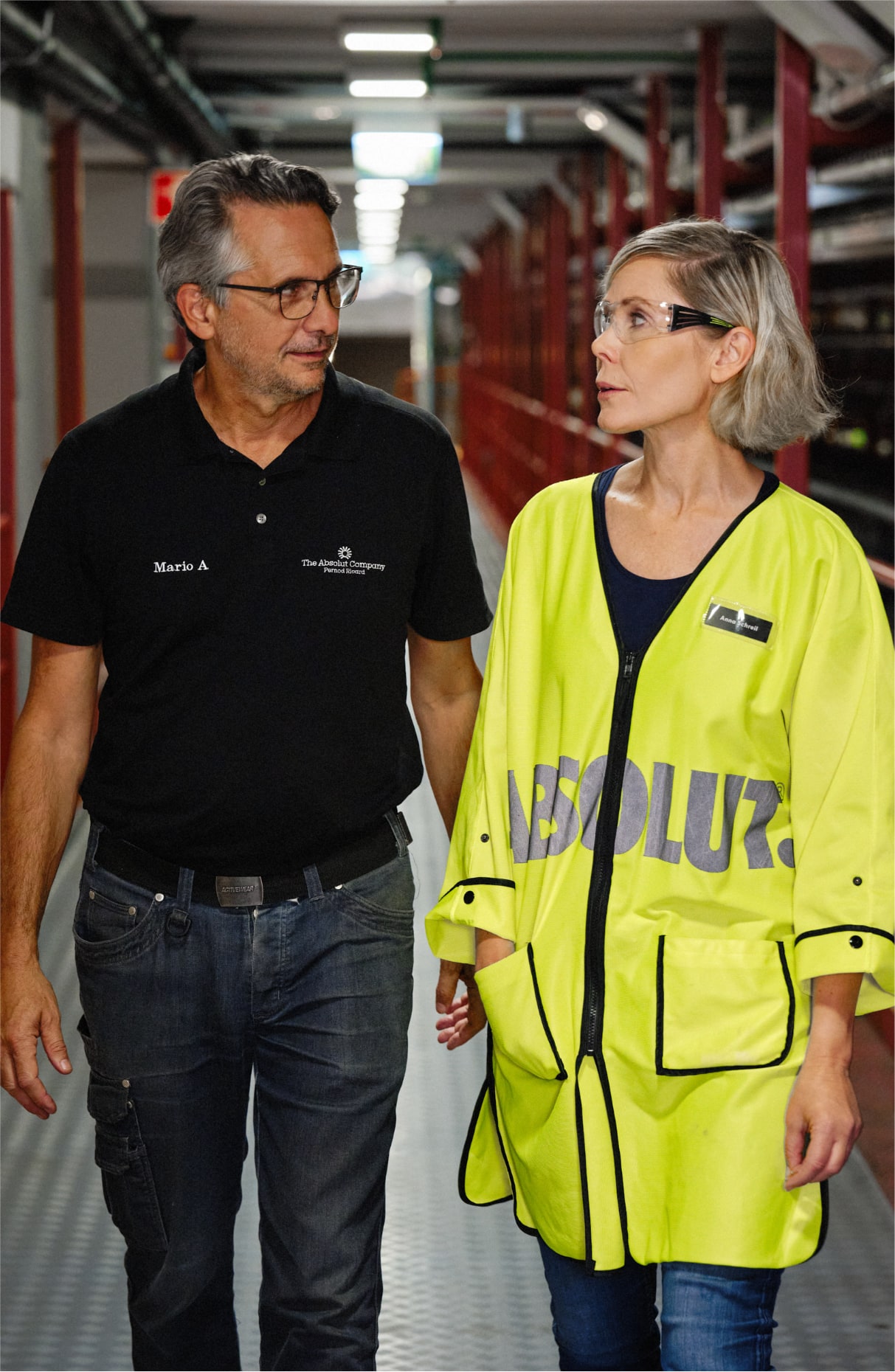
We remain one of the most energy-efficient distilleries in the world. This year our distillery in Nöbbelöv, close to Åhus, is 94 per cent more carbon efficient and emits seventeen times less CO2 per litre of alcohol than the average distillery**. As part of a previous commitment for our facilities to be fossil-free by 2025, we continue to phase in renewable fuels, one of them being our own waste spirits, to replace the remaining fossil fuels at the distillery.
As VP of Operations, Anna oversees every step of sourcing and manufacturing for Absolut Vodka, including distilling, blending, bottling and distributing. By her admission, she is obsessed with waste, efficiency and optimisation. “I love efficiency, I love circularity and despise waste. I want to work smarter, not harder,” she says. “I’ve always been obsessed with minimising losses with the production process – time losses, quality losses, health and safety losses and material losses.”
Anna points to a new two million litre storage facility being built as an example of increased efficiency and optimisation. The new facility will enable the distillery to maximise output by keeping it running during periods of lower demand because while it is continually running, it is at its most energy efficient. “To run the operation optimally you need to have maximum, constant output. You can’t keep producing when there is demand but you have nowhere to store the product. You have to turn production on and off as demand fluctuates, which is energy inefficient. We are increasing our storage capacity by 20 per cent to optimise our processes even further,” says Anna.
Breaking ground with glass
Almost half of the carbon footprint of Absolut Vodka comes from the natural gas used in the production of the bottle but a major new ground-breaking project aims to change this. Working with Ardagh, our long-term glass bottle supplier, we are soon to test a partly-hydrogen-fired glass furnace for large-scale production in a move that will reduce our CO2 emissions considerably. This is just the start.
“Our collaboration is bold and, I’d say quite audacious. This is a step change, not a revolution. We also need to think about furnaces of the future that can only run on electricity, for instance,” adds Anna.
Recycling continues to be a major part of our philosophy of being circular and in FY23 our glass bottles were confirmed 100 per cent recyclable in Sweden while we currently use at least 45 per cent recycled glass, known as cullet (recycled glass) in our Absolut Vodka bottles. This level of recycled glass has both increased and fallen slightly in the past year. It increased to 53 per cent but reduced to 44 per cent as supplies for recycled glass in Sweden fell. We anticipate this to be a short-term situation and still aim to increase our recycled content to 60 per cent by 2025. Increasing recycled content, not only supports a sustainable circular economy in Sweden but also reduces carbon emissions, mainly because less energy is needed to melt the raw material.
Optimising containers
Our obsession with optimising our shipping containers continues. Over the past few years, our warehouse team have been working studiously to optimise how we load our containers. It has been a while since we have used wooden pallets in containers, using slip sheets instead, and we have persuaded other markets to follow suit. “It is about load optimisation for every single case that we can stuff into a container as tightly as we can. This immediately makes a direct impact from an environmental and cost point of view,” says Anna.
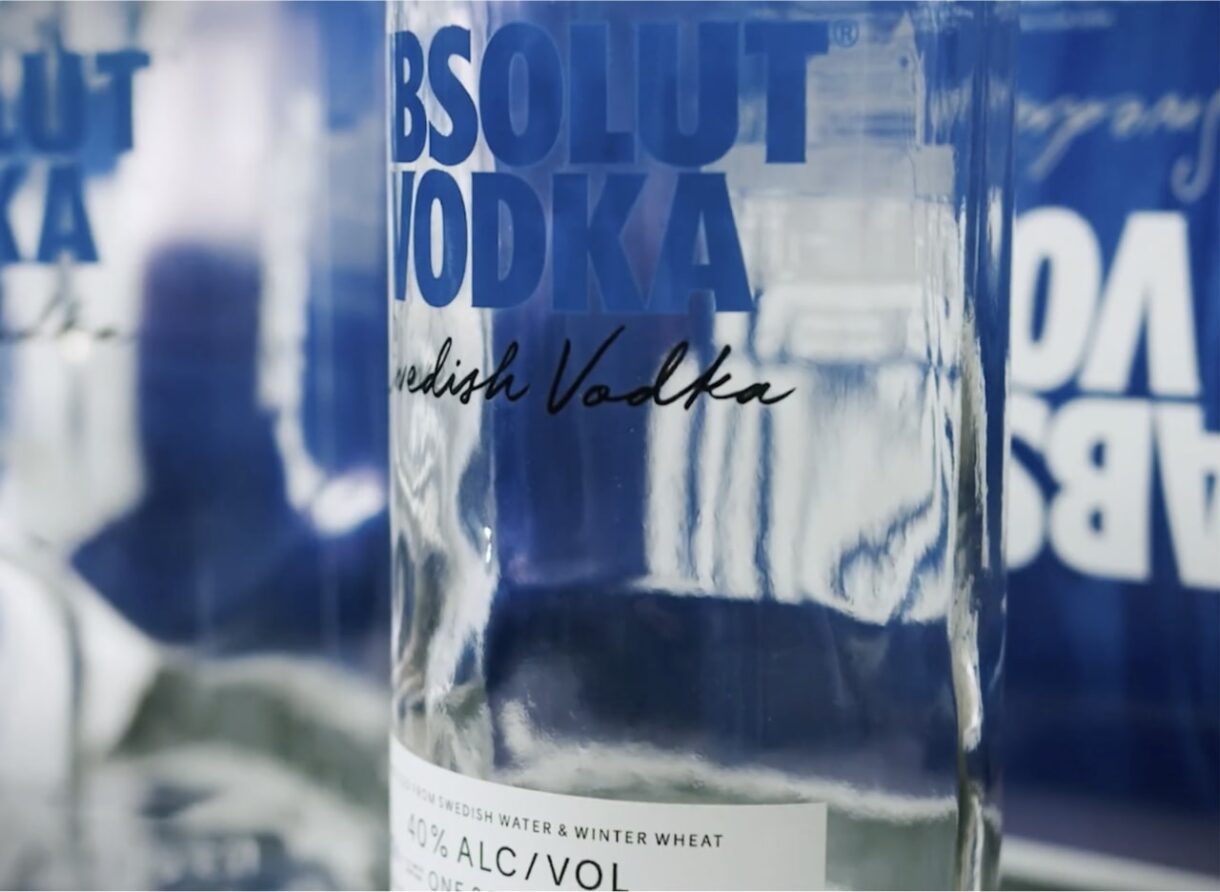
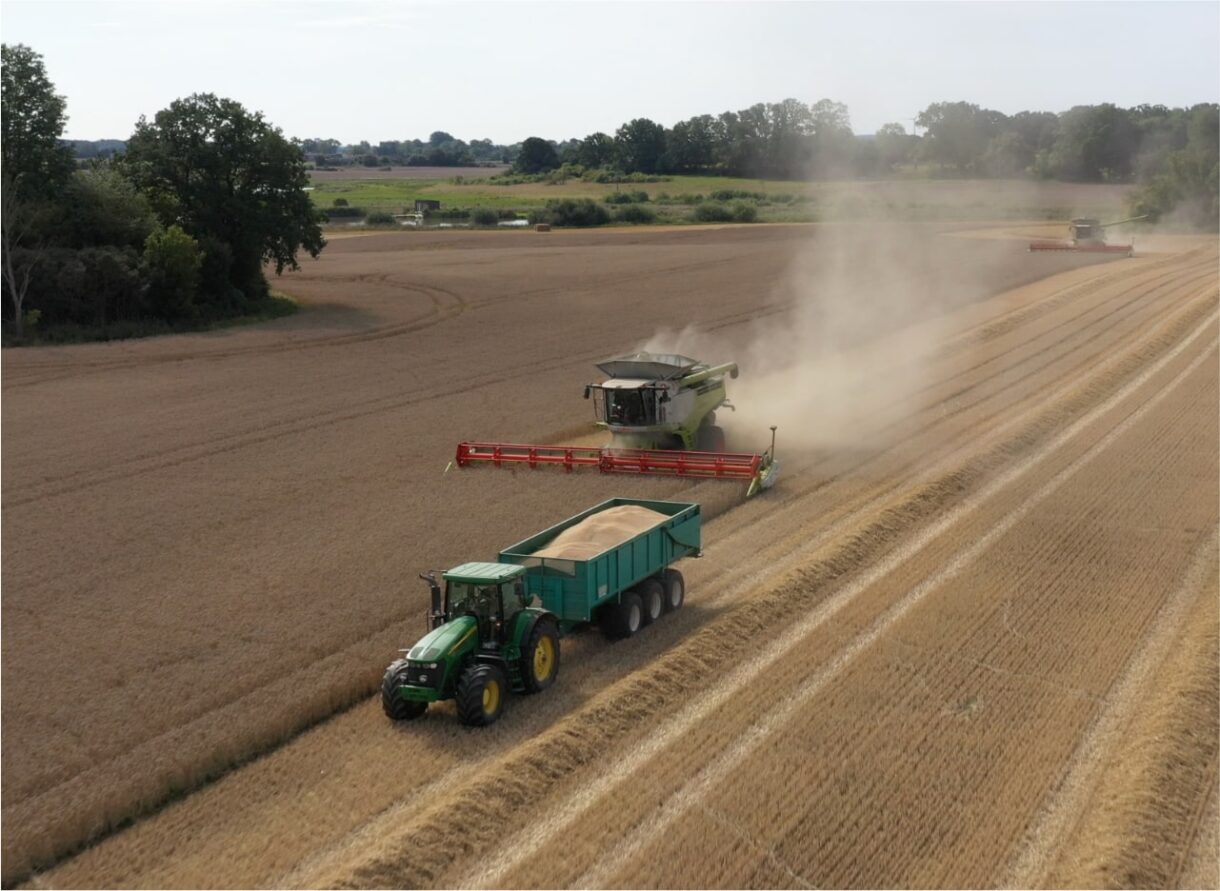
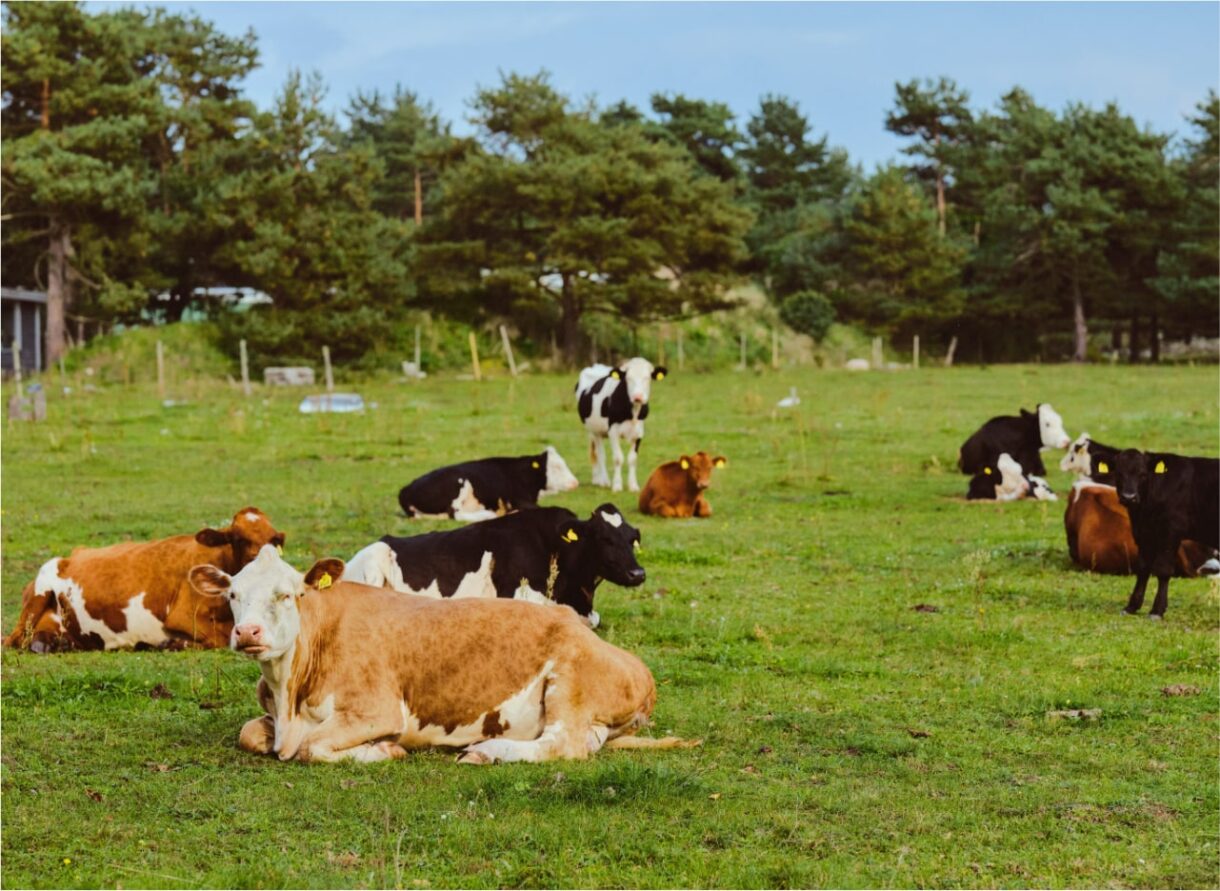
Carbon capture challenge
We are on track to be carbon neutral by 2030 and apart from reducing our footprint, carbon capture will be a main lever for us to achieve this. We are now working on solutions for actually removing CO2 from the air, both at the distillery and in the cultivation of wheat.
At our distillery, biogenic CO2 (captured from the air by the growing wheat) is released as part of the wheat fermenting process. Some of it is collected, liquefied and sold to other industries. However, we see the potential of collecting more and also joining the current drive to safely stow away the CO2 in long-term storage using Bio-Energy Carbon Capture and Storage (BECCS). “We capture approximately 30 per cent of the biogenic CO2 from fermentation but we want to go higher and we need to have a system to fulfil this goal,” adds Anna.
Some of the CO2 which is captured in the wheat as it grows actually remains in the soil after the harvest. Models and calculations determining the amounts of carbon that are stored are evolving. Still, we do know that some of the actions we incentivise in our Wheat Sustainability Programme, such as cover crops and the use of organic fertilisers, are beneficial to the sequestration of carbon.
Global dynamics have changed – the landscape is, arguably, more unpredictable than ever. We have leaned on our experiences since 2020 to adapt as we continue on our journey to be carbon neutral by 2030. “Over decades we mastered being super-efficient during long bouts of predictability,” says Anna. “Today, we need to be ambidextrous in our thinking. If our right hand is our ability to be super-efficient when things are predictable, we need our left hand to be super agile when times are volatile. We need to master shifting our mindset to one of flexibility, to optimise our processes at the flick of a switch.”

Today, we need to be ambidextrous in our thinking. If our right hand is our ability to be super-efficient when things are predictable, we need our left hand to be super agile when times are volatile. We need to master shifting our mindset to one of flexibility, to optimise our processes at the flick of a switch.
— Anna Schreil, VP of Operations
* Calculated using market-based approach.
** Average data from 2020. Beverage Industries Environmental Roundtable (BIER) benchmarking study.