A safe pair of hands
When he’s not lifting weights in his garage, Mikko Niemi, operations director at Pernod Ricard Finland Oy, now part of The Absolut Group, is always thinking logically and striving to empower his colleagues to dare to try.
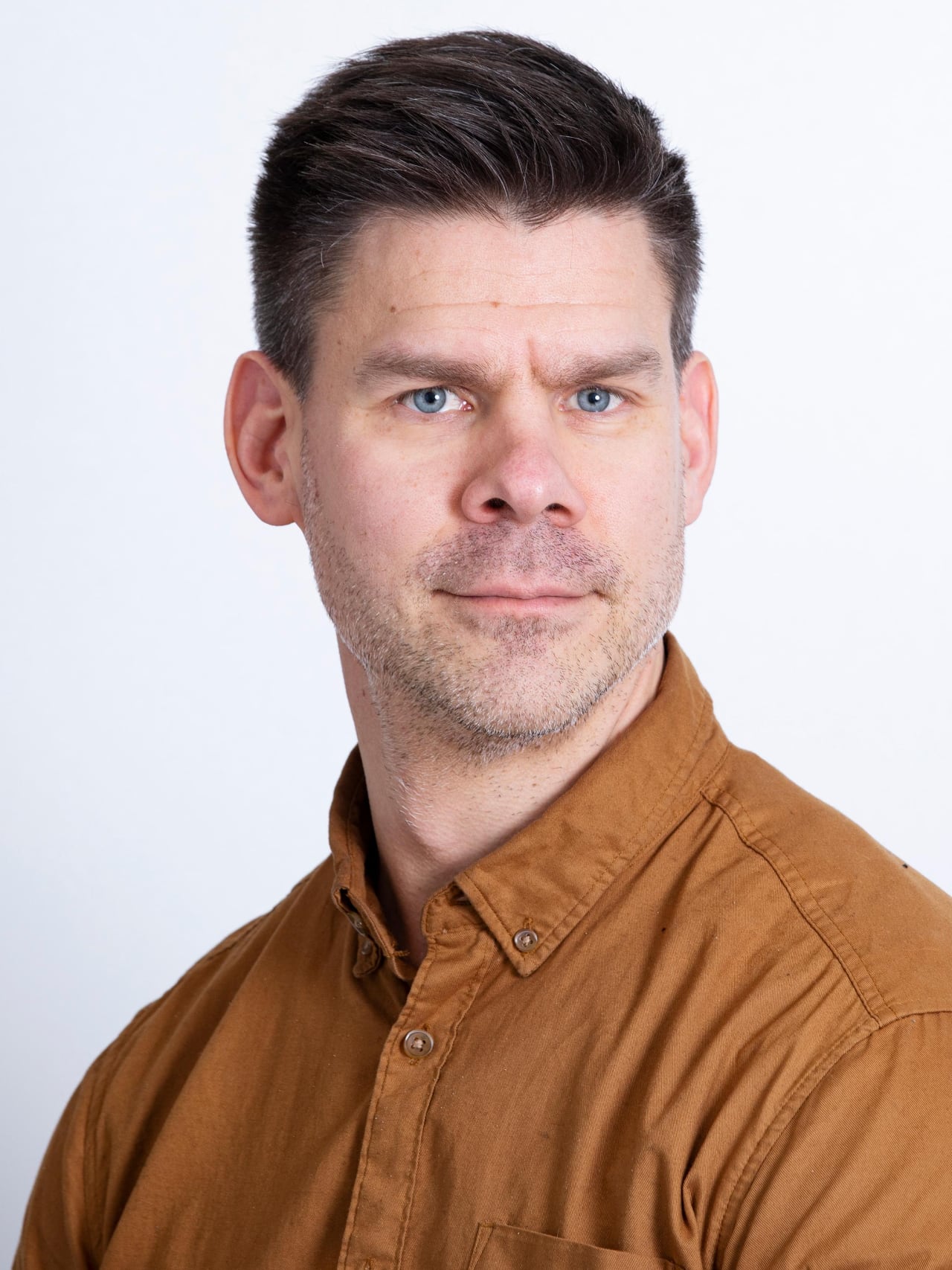
We sat down with Mikko to discover what motivates him, how he leads his team and why he keeps his emotions to himself.
You’ve spent most of your career at Pernod Ricard Finland – what attracted you in the first place?
I graduated in food technology, but the local butter factory never really appealed! I was always interested in how drinks were made such as the popular spiced liqueur, Minttu. So, when I saw a job advertised for a bottling supervisor at Vin & Sprit, I jumped at the chance to apply. When I got a call for an interview, I happened to be on national service at a forest camp. Fortunately, my captain gave me leave so I could go to the interview. I gained invaluable leadership experience during my army year that’s for sure. It gave me exposure to managing people out of their comfort zone. We were often put in tough situations – where you get little sleep or food or are exhausted from the hard physical training – very different from everyday workplace environments.
What products are produced in Pernod Ricard Finland?
At our facility in Turku, we mainly produce products for the Nordic markets – we are the second-largest player in the Finnish spirits industry, for instance – producing more than 100 different drinks for Nordic markets including fortified wines, berry liqueurs and vodka products. We do export and this includes our peppermint-flavoured Minttu, which is one of our most popular liqueurs. From the TAG portfolio, we produce Absolut RTD, Malfy Gin & Tonica RTD and blending and bottling Beefeater Gin.
What is your vision for the Turku operations now you are part of TAG?
We already have more global projects and my vision is for our factory to be utilised even more for international projects because we have lots of capabilities that other factories may not have. For example, we manufacture many RTDs with lower ABVs while we can manufacture products both with intense flavours such as Minttu or others with less intensity, or very little flavour.
How do you approach your director of operations role?
My philosophy is to do the same thing but better and better. Consistency is crucial for production and our focus is to run the perfect process. It is so much more important than doing something very spectacular just once. We have meetings every day (and I try to join as many as I can) to go through the production agenda as well as health and safety updates. There is also a great deal of planning to be done – particularly with new products, which I am heavily involved in, to oversee the costs and to ensure that our operations are being fully and efficiently utilised.
How would your colleagues describe your leadership style?
I’d guess they would say that I am predictable and calm but fair – I’m not sure many people have ever seen me lose my temper. I’m a logical thinker so not full of surprises! I try to leave emotion aside, which I think is important when it comes to production. When something doesn’t work, rather than scream “Why the hell has this happened” it’s better to step back and try to work out why is it not working, than blow a fuse. Besides, it is symptomatic of a production line that there will always be challenges and issues. I believe that you are better embracing and working through them – this will ease the burden and make your life a great deal less stressful!
Do you have any role models when it comes to leaders and leadership?
I have been part of many different management teams with different styles. Naturally, some managers have had traits that are not necessarily the way I would manage but I always observe and take influence where I can – such as learning from leaders who are great at motivating people. What I would say is that having been here for 18 years, leadership has improved – managers are more holistic and have a wider view of how to lead and bring the best out of people.
My philosophy is to do the same thing but better and better. Consistency is crucial for production and our focus is to run the perfect process. It is so much more important than doing something very spectacular just once.
Describe the culture and values in Finland
Aligned with the Pernod Ricard Group, we share the value of encouraging each other rather than judging. With new projects, there will always be a degree of trial and error, but we mustn’t be afraid of making mistakes. We encourage our colleagues to rise to the challenge without the fear of failure. We are also increasingly embracing a safety culture, one where managers need to guide and be able to think through the “safety glasses” in various situations. Health and safety is a topic that is discussed every day in our morning meetings and is also reinforced by the Group’s care visit initiative, where managers go to the workplace to speak to their colleagues to find out what concerns them.
What continues to motivate you some 18 years on?
I love the job. There is always a challenge with new products being launched regularly. I enjoy crafting ideas and seeing projects come alive. For example, a project for Malfy Gin & Tonica RTD was technically challenging because we had to place stickers on the mottled surface of the bottle. The mentality we have here is to be innovative, knowing that challenges can be overcome. Production is also a long journey. You can’t change targets too often because you have to invest in machines and people. Everything and everyone evolves in the factory and you get to see it firsthand. That’s why I have liked being here for such a long time because you are part of the journey.
How does Pernod Ricard Finland approach sustainability?
Much like the Pernod Ricard Group, achieving carbon neutrality is at the forefront of our minds. Our energy supplier Turku Energia generates all the energy our production facility industrial area needs by using wood chips sourced locally and our site has been solely using renewable energy since 2019. We offer products in PET bottles for the Nordic markets as we look to reduce our emissions. The alcohol monopolies in Sweden (Systembolaget) and Finland (Alko) have announced targets to lower their scope 3 emissions, and they are encouraging the drinks industry to switch from glass to PET. We have undertaken several projects in this regard – Beefeater Gin, for example, is sold in PET bottles bottled in Turku for the Nordic markets, where recycling is very well managed.
How do you unwind away from the factory?
As a student of food technology, I like to cook and eat good food of course! Having just built a house, my family also keeps me busy – I have two young children and two dogs. I can escape to a small gym in my garage to do some weight training, although the days of bench-pressing “200kg” are long gone!
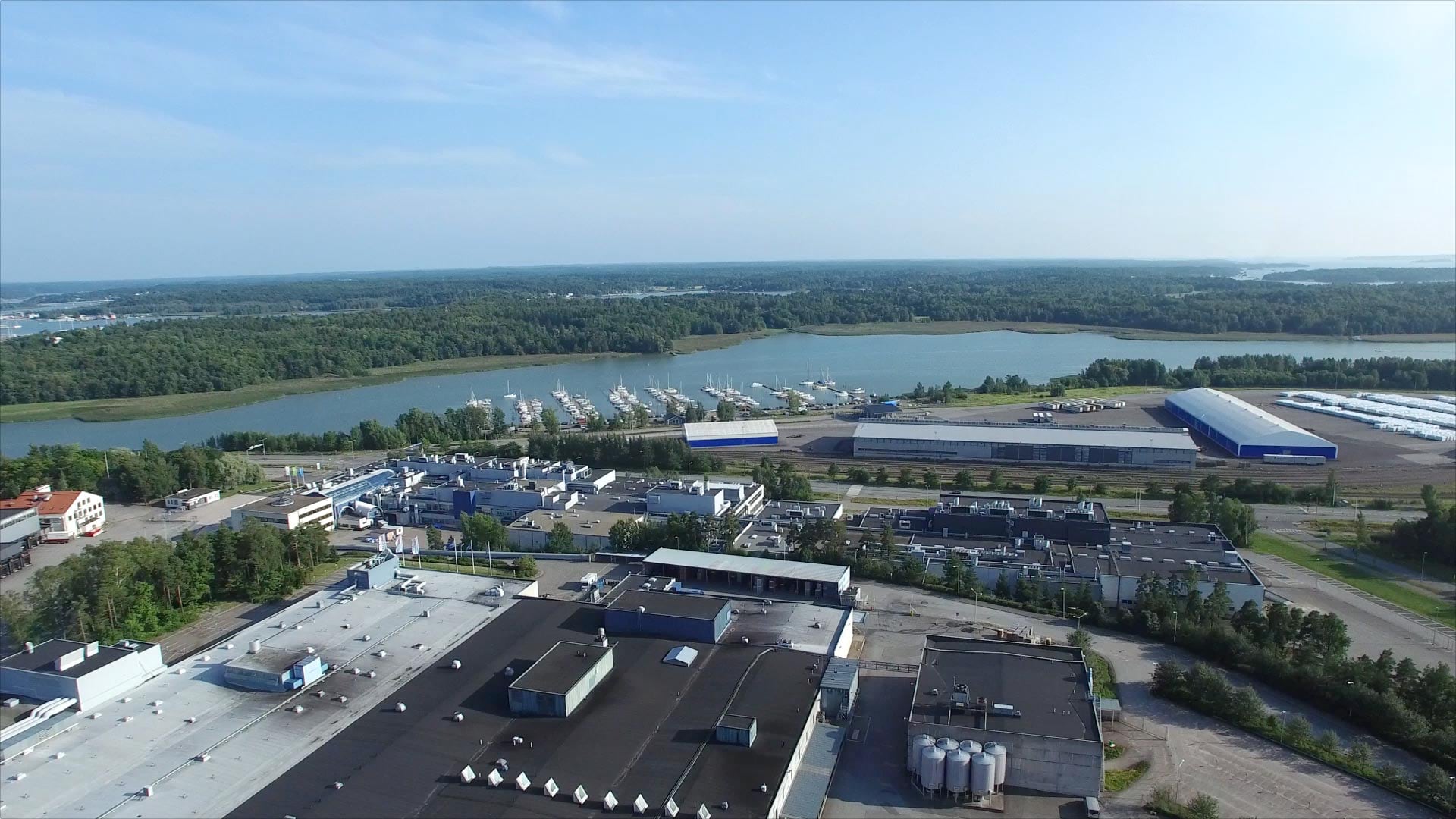